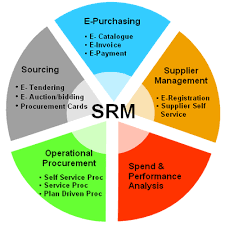
Business process management is a discipline which focuses on improving business processes, and automating them. Various methods are used in this field to achieve this goal. The basic concepts of business process management include: modeling, automation, and observability. You can read this article to learn about the many benefits of business processes management.
Business process management
BPM (Business Process Management) allows companies to manage complexity while making flexible changes that are beneficial for customers. It utilizes data-driven information in order to improve business processes. This is an effective way for a company to succeed long-term. BPM is a digital transformation tool that helps companies stand out from their competitors.
A business process can be described as a series or sequence of events, tasks, and workflows that happen in a business. It is an integral part in running a company. An organization might have a standardized onboarding process to make sure that employees are able to transition smoothly to their new job. This would include documentation and training materials, checklists, and agreements. These tasks can also be automated.
Business process modeling
Business process modelling is a way to analyze and automate processes. This process is useful for many reasons. It helps you identify waste and optimize processes. It can also help you gain a better understanding of your business and determine areas that need improvement. It is a process that will save you time and money.
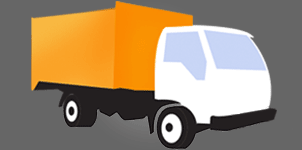
There are many tools and techniques that can be used to facilitate process modeling. One such tool is value stream modeling, which highlights the most important steps and the flow and information of the process. This method is also called input-process and output modeling. Process flow can be described as a functional graph that has inputs and outputs.
Orchestration of business processes
Orchestration refers to the coordination of the execution of various processes. Orchestration is a collaborative effort. It requires that all participants have an understanding of the business and its operations. The process coordinator plays a central role in orchestration. This technique is also used to incorporate web-services into larger business process. It makes it possible to plan alternate scenarios in the case of mishaps.
Process orchestration is still a relatively new technology. Few automation tools are marketed today as orchestration engines. This tool's ability to manage multiple processes is what makes them unique. Some orchestration software includes REST API adapters that allow for reuse of tasks.
Monitoring of business processes
A program called business process monitoring can be used to monitor different business processes. It is an application that can be installed on computer systems. It can be used to help organizations identify and fix any business processes that are not working well. Moreover, it can also help improve the quality of a service or product. It is easy to install on any computer system and is available for purchase.
Monitoring business processes allows companies to identify the root cause and fix the problem. In turn, business process monitoring increases a company's productivity and efficiency.
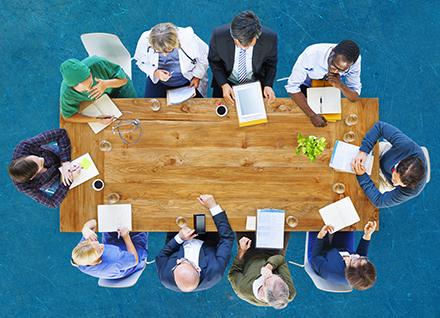
Improvement of business processes
Business process improvement can be used to improve the efficiency and effectiveness of a business's operations. The basic principles of business improvement are to reduce inefficiencies, maximize performance time and maximize efficiency. The first step to identifying problem areas and finding solutions is the most important. Employees and stakeholders are required to be involved in improving business processes. It may involve introducing new systems or teams or re-designing existing processes. To minimize risks, it is important to test any changes.
Business process improvement can help companies increase the quality of their products and services. A high-quality product means satisfied customers. This leads to more sales. Additionally, happy customers are likely to become repeat customers, which means increased revenue.
FAQ
How does a manager motivate their employees?
Motivation is the desire to do well.
Engaging in something fun can be a great way to get motivated.
You can also feel motivated by making a positive contribution to the success in the organization.
If you are a doctor and want to be one, it will likely be more rewarding to see patients than to read medical books every day.
Motivation comes from within.
For example, you might have a strong sense of responsibility to help others.
You might even enjoy the work.
Ask yourself why you feel so motivated.
Then try to think about ways to change your situation to be more motivated.
What are the steps in the decision-making process in management?
Managers are faced with complex and multifaceted decisions. It involves many factors, including but not limited to analysis, strategy, planning, implementation, measurement, evaluation, feedback, etc.
It is important to remember that people are human beings, just like you. They make mistakes. As such, there is always room for improvement, especially if you're willing to put forth the effort to improve yourself first.
This video explains the process of decision-making in Management. We will discuss the various types of decisions, and why they are so important. Every manager should be able to make them. Here are some topics you'll be learning about:
How do you define Six Sigma?
Six sigma is a common concept for people who have worked in statistics or operations research. Anyone involved in business can benefit.
This requires a lot of dedication, so only people with great leadership skills can make the effort to implement it.
Statistics
- 100% of the courses are offered online, and no campus visits are required — a big time-saver for you. (online.uc.edu)
- The BLS says that financial services jobs like banking are expected to grow 4% by 2030, about as fast as the national average. (wgu.edu)
- Our program is 100% engineered for your success. (online.uc.edu)
- As of 2020, personal bankers or tellers make an average of $32,620 per year, according to the BLS. (wgu.edu)
- This field is expected to grow about 7% by 2028, a bit faster than the national average for job growth. (wgu.edu)
External Links
How To
How does Lean Manufacturing work?
Lean Manufacturing is a method to reduce waste and increase efficiency using structured methods. They were created in Japan by Toyota Motor Corporation during the 1980s. It was designed to produce high-quality products at lower prices while maintaining their quality. Lean manufacturing is about eliminating redundant steps and activities from the manufacturing process. It includes five main elements: pull systems (continuous improvement), continuous improvement (just-in-time), kaizen (5S), and continuous change (continuous changes). Pull systems are able to produce exactly what the customer requires without extra work. Continuous improvement is the continuous improvement of existing processes. Just-in-time is when components and other materials are delivered at their destination in a timely manner. Kaizen is continuous improvement. This can be achieved by making small, incremental changes every day. The 5S acronym stands for sort in order, shine standardize and maintain. To achieve the best results, these five elements must be used together.
Lean Production System
Six key concepts underlie the lean production system.
-
Flow - focuses on moving information and materials as close to customers as possible.
-
Value stream mapping - Break down each stage in a process into distinct tasks and create an overview of the whole process.
-
Five S’s - Sorted, In Order. Shine. Standardize. And Sustain.
-
Kanban - visual cues such as stickers or colored tape can be used to track inventory.
-
Theory of Constraints - Identify bottlenecks in the process, and eliminate them using lean tools such kanban boards.
-
Just-intime - Order components and materials at your location right on the spot.
-
Continuous improvement - make incremental improvements to the process rather than overhauling it all at once.