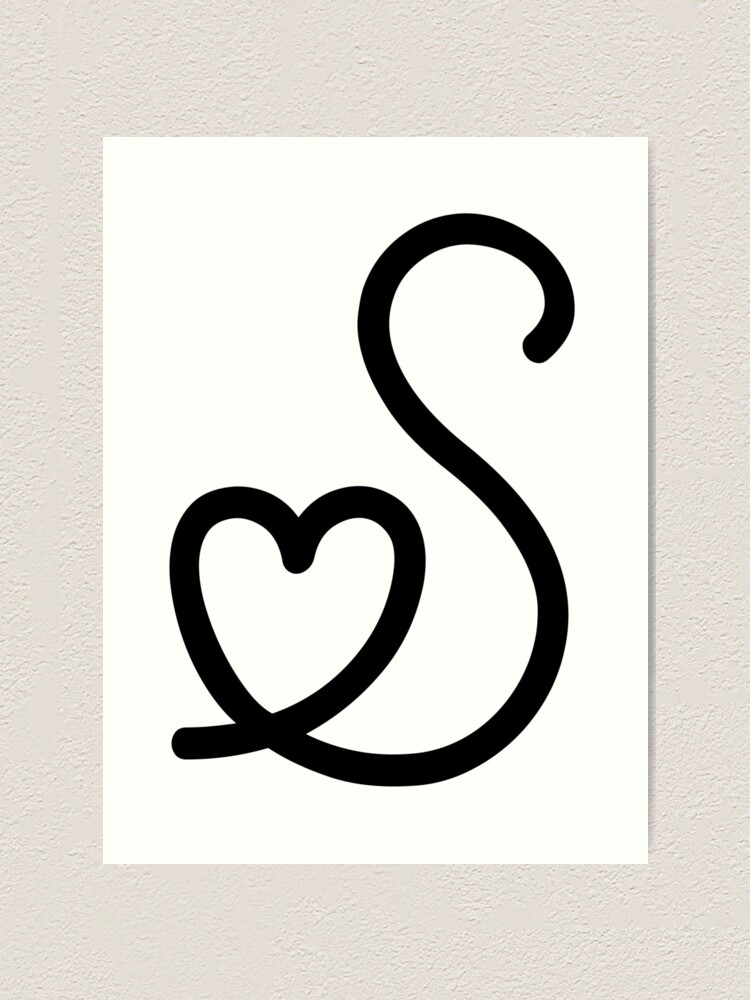
Multiple studies have been carried out to explore the dynamic of work flexibilty. They examined the effect of flexible working arrangements on organizational productivity and performance, as well as the relationship between flexibility and job satisfaction. They also examined the effects of flexible working arrangements on employee wellbeing. They have also examined the benefits to employees and employers.
These studies provided valuable insights into the effect of work flexibility on employees' performance. They have found that employees who have flexible working arrangements have higher job satisfaction, performance, and health, and are also better able to manage their personal and professional lives. Employees who have flexible work arrangements have better preventive and social skills than those who have permanent jobs.
This study also explores the impact of flexible working arrangements on the wellbeing and performance of employees, focusing on the four main types of work flexibility. These types include: working time flexibility, working space flexibility, urgent management measures, and functional flexibility. Using a comparative analysis of the extant literature, the study explores the impact of different forms of work flexibility on the performance of employees.
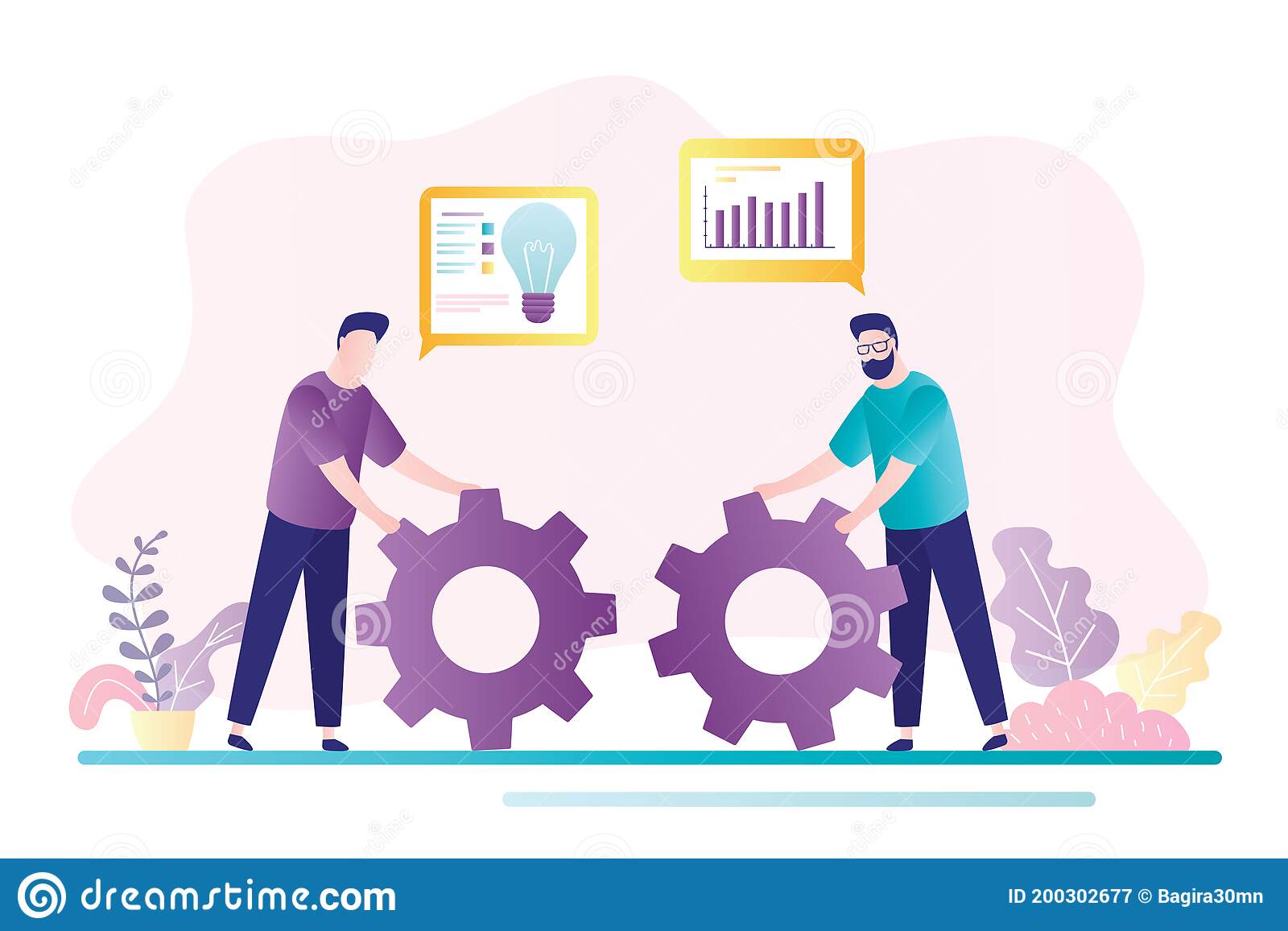
Flexibility in working arrangements has a positive impact on employees' productivity, wellbeing, and organizational performance. This research was based upon the views of Romanian employees. To get the opinions of the employees, the study employed multiple correspondence analysis (MCA). MCA is a statistical technique that measures the magnitude of the explanation of variance in factorial scores. The MCA approach differs from the PCA one in that the dependent variables are not observed. Its assumption is that the information is used to generate a composite indicator.
The MCA approach identifies the first axis as the ordering consistency principle of the factorial scores. It is expected that the factorial scores of the first axis would increase in time. The coefficients for this axis have higher probabilities than the threshold of 10% significance.
The key findings reveal that the composite indicator of employee flexibility includes functional flexibility, flexibility in working hours and flexibility in working spaces. Urgent management measures are also important. These three elements are especially important for job performance, job satisfaction and job satisfaction.
The study analyzes the effects of different work flexibility options on employee performance, job happiness, and organizational performance. This study also highlights the importance of new workspaces for job performance and job satisfaction. This study found that new types of workspaces can lead to better organizational performance and job performance as well as employee motivation, satisfaction, and retention.
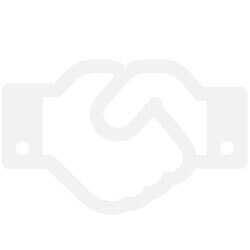
A comparative analysis of data showed that functional flexibility, flexibility in working spaces, and flexibility in working time was strongly linked to each other. The correlation between these factors has been determined using a binary logistic regression model. This model was validated using the Hosmer & Lemeshow test. This test confirms that the model accurately describes the data.
FAQ
What is the difference between TQM and Six Sigma?
The main difference between these two quality-management tools is that six-sigma concentrates on eliminating defects while total QM (TQM), focuses upon improving processes and reducing expenses.
Six Sigma can be described as a strategy for continuous improvement. This approach emphasizes eliminating defects through statistical methods like control charts, Pareto analysis, and p-charts.
This method seeks to decrease variation in product output. This is done by identifying root causes and rectifying them.
Total quality management includes monitoring and measuring all aspects of an organization's performance. It also involves training employees to improve performance.
It is commonly used as a strategy for increasing productivity.
How do we create a company culture that is productive?
A successful company culture is one that makes people feel valued and respected.
It's founded on three principal principles:
-
Everyone has something valuable to contribute
-
People are treated fairly
-
Respect is shared between individuals and groups
These values can be seen in the behavior of people. They will show consideration and courtesy to others.
They will be respectful of the opinions of other people.
They can also be a source of inspiration for others.
In addition, the company culture encourages open communication and collaboration.
People are free to speak out without fear of reprisal.
They understand that errors will be tolerated as long they are corrected honestly.
Finally, the company culture promotes honesty and integrity.
Everyone knows that they must always tell the truth.
Everyone understands there are rules that they must follow.
Nobody expects to be treated differently or given favors.
What are the steps in the decision-making process in management?
The decision-making process of managers is complicated and multifaceted. This involves many factors including analysis, strategy and planning, implementation, measurement and evaluation, feedback, feedback, and others.
Management of people requires that you remember that they are just as human as you are, and can make mistakes. As such, there are always opportunities for improvement, especially when you put in the effort to improve yourself.
This video explains the process of decision-making in Management. We discuss different types of decisions as well as why they are important and how managers can navigate them. The following topics will be covered.
What does Six Sigma mean?
Six Sigma uses statistical analysis for problems to be found, measured, analyzed root causes, corrected, and learned from.
The first step in solving a problem is to identify it.
The data is then analyzed and collected to identify trends.
The problem can then be fixed by taking corrective measures.
Finally, data is reanalyzed to determine whether the problem has been eliminated.
This continues until you solve the problem.
What is a fundamental management tool for decision-making?
The decision matrix is a powerful tool that managers can use to help them make decisions. It allows them to consider all possible solutions.
A decision matrix can be used to show alternative options as rows or columns. It is easy to see how each option affects the other options.
We have four options in this example. They are represented by the boxes to the left of the matrix. Each box represents a different option. The top row displays the current situation, and the bottom row shows what might happen if nothing is done.
The middle column shows the effect of choosing Option 1. It would increase sales by $2 million to 3 million in this instance.
These are the results of selecting Options 2 or 3. These are both positive changes that increase sales by $1million and $500,000. These positive changes have their downsides. Option 2 increases the cost of goods by $100,000. Option 3 decreases profits and makes them less attractive by $200,000.
The final column shows the results for Option 4. This would result in a reduction of sales of $1 million.
The best thing about a decision matrix is the fact that you don't have to remember which numbers go with what. It's easy to see the cells and instantly know if any one of them is better than another.
This is because the matrix has already taken care of the hard work for you. It is as simple as comparing the numbers within the relevant cells.
Here is an example how you might use the decision matrix in your company.
It is up to you to decide whether to spend more money on advertising. By doing so, you can increase your revenue by $5 000 per month. However, this will mean that you'll have additional expenses of $10,000.
If you look at the cell that says "Advertising", you can see the number $15,000. Advertising is worth more than its cost.
Statistics
- Hire the top business lawyers and save up to 60% on legal fees (upcounsel.com)
- 100% of the courses are offered online, and no campus visits are required — a big time-saver for you. (online.uc.edu)
- The profession is expected to grow 7% by 2028, a bit faster than the national average. (wgu.edu)
- UpCounsel accepts only the top 5 percent of lawyers on its site. (upcounsel.com)
- The BLS says that financial services jobs like banking are expected to grow 4% by 2030, about as fast as the national average. (wgu.edu)
External Links
How To
How does Lean Manufacturing work?
Lean Manufacturing techniques are used to reduce waste while increasing efficiency by using structured methods. They were created in Japan by Toyota Motor Corporation during the 1980s. It was designed to produce high-quality products at lower prices while maintaining their quality. Lean manufacturing emphasizes removing unnecessary steps from the production process. It includes five main elements: pull systems (continuous improvement), continuous improvement (just-in-time), kaizen (5S), and continuous change (continuous changes). Pull systems involve producing only what the customer wants without any extra work. Continuous improvement is the continuous improvement of existing processes. Just-in time refers to components and materials being delivered right at the place they are needed. Kaizen is continuous improvement. This can be achieved by making small, incremental changes every day. Fifth, the 5S stand for sort, set up in order to shine, standardize, maintain, and standardize. These five elements work together to produce the best results.
Lean Production System
Six key concepts make up the lean manufacturing system.
-
Flow - focus on moving material and information as close to customers as possible;
-
Value stream mapping: This is a way to break down each stage into separate tasks and create a flowchart for the entire process.
-
Five S's – Sort, Put In Order Shine, Standardize and Sustain
-
Kanban: Use visual signals such stickers, colored tape, or any other visual cues, to keep track your inventory.
-
Theory of constraints - identify bottlenecks during the process and eliminate them with lean tools like Kanban boards.
-
Just-in time - Get components and materials delivered right at the point of usage;
-
Continuous improvement: Make incremental improvements to the process instead of overhauling it completely.