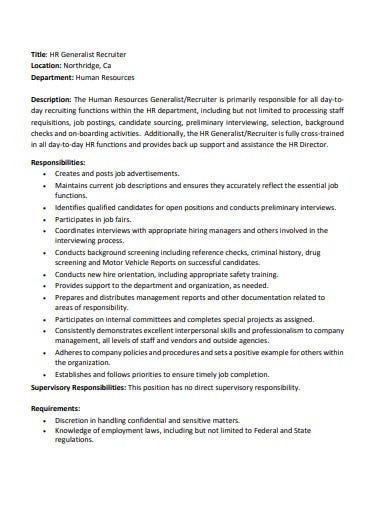
Proper waste management must always be taken into consideration when managing chemical waste or manufactured waste. Incompatible chemicals should be stored in separate secondary containment bins to prevent the formation of toxic fumes and aerosols. Additionally, incompatible chemicals should not be mixed with other chemicals, which may cause explosions and fires.
Hazards
To prevent health and environmental hazards, it is important to properly dispose of chemical waste. Proper disposal includes identifying the streams of chemical waste that should be disposed. This usually happens at the end of an experiment. In certain cases, hazardous materials may be mixed in with normal waste to save money. This is not an option.
You must ensure that the MSDSs of hazardous chemicals are checked before you store them. These MSDS can often be found online or at the manufacturer. These include the hazard information for a chemical, as well as its composition. They also include emergency procedures that can be used to manage a spillage.
Regulations
Chemical waste management rules govern chemical waste disposal in all workplaces, from manufacturing plants to laboratories. While most chemical wastes are created in laboratories, there are some other types that are not related to the laboratory. These include contaminated soils, building materials, paints and lubricants. Expired chemicals can also be disposed off according to rules.
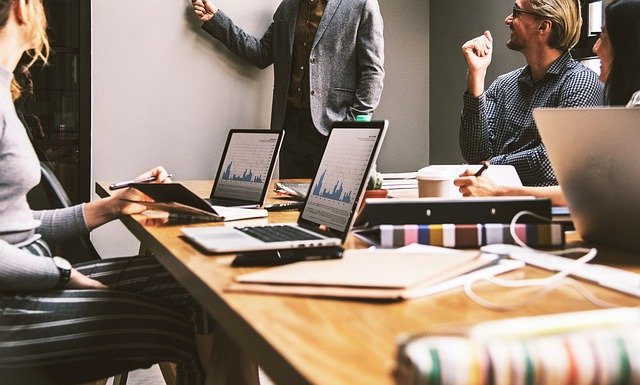
The proper handling of hazardous wastes is an integral part of safety protocols and is the responsibility of employees. This is done to limit personal exposure and reduce the potential for environmental contamination. Two University programs are available to assist employees with complying with regulations.
Collection
First, fill out the Chemical Collection Form. This form needs to be completed for each trash container. Often, multiple containers of the same chemical waste are combined into a single request. The form can be submitted online. You will then receive your CCR number as well as a Dangerous Waste label. Once you have this information, you can print it and attach it to the waste container's label.
Chemical wastes include any substance no longer being used or a mixture thereof. These materials can be in solid, liquid, or gaseous form. To avoid pollution charges, it's important to properly dispose of chemical waste.
Storage
To avoid contamination, it is essential to have proper storage procedures for chemical waste. Separate wastes according the hazard type to avoid contamination. You should store them in compatible containers. Hydrofluoric acid-containing chemical wastes should not be kept in metal or glass containers. For liquids-containing wastes, containers should be designed for liquids. If the containers are too small to hold large quantities, they should transfer to larger containers.
Containers should also be sealed tightly. Containers should be sealed tightly to prevent leakage. Containers that contain contaminated glassware should be puncture-proof. Hazardous waste should be clearly marked on the containers.
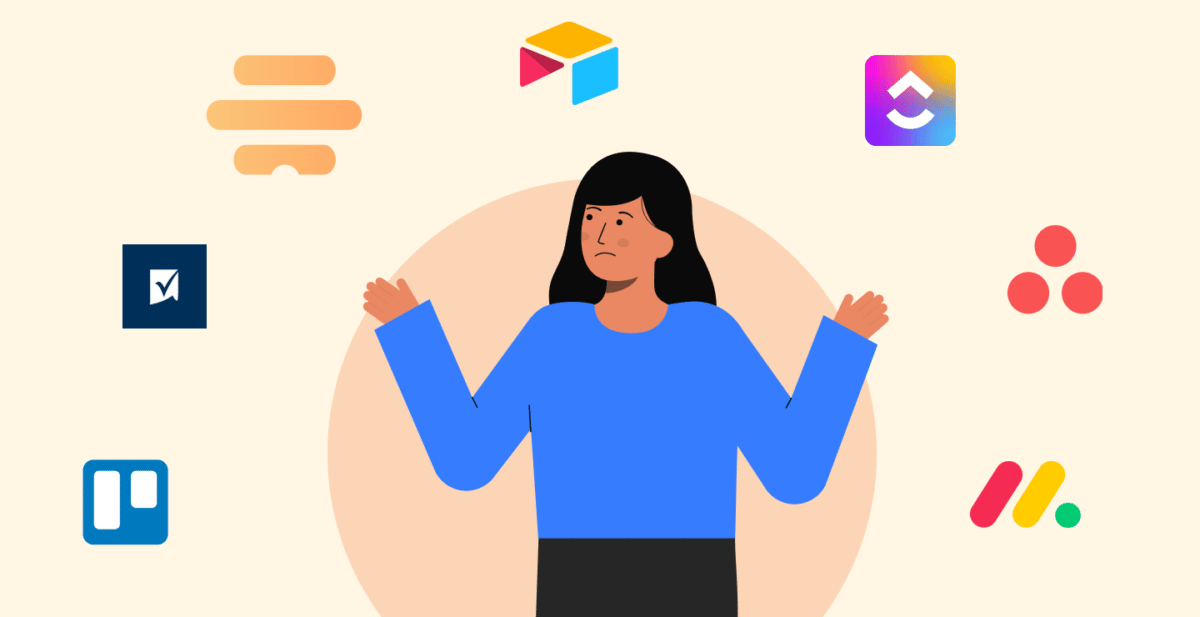
Disposal
It is important to be familiar with the proper disposal process if your company produces hazardous waste. The Texas Commission on Environmental Quality, as well as the Environmental Protection Agency regulate hazardous wastes. Improper disposal could result in heavy fines and even legal action. This type waste should be properly managed by a hazardous waste management company.
Chemical waste is the waste of chemicals that have no further use. These chemicals come in many different forms. Some of these wastes are hazardous while others are safe. Some chemical wastes can be universally hazardous while others may be household hazardous. For a chemical to be considered hazardous, it must demonstrate four characteristics. They may be radioactive, toxic or flammable. Some chemicals must be stored in special containers for safe disposal.
FAQ
Six Sigma is so beloved.
Six Sigma is easy and can deliver significant results. It provides a framework that allows for improvement and helps companies concentrate on what really matters.
Why is it so hard to make smart business decisions?
Complex systems and many moving parts make up businesses. It is difficult for people in charge of businesses to manage multiple priorities simultaneously and also deal with uncertainty.
To make good decisions, you must understand how these factors affect the entire system.
This requires you to think about the purpose and function of each component. It's important to also consider how they interact with each other.
It is also worth asking yourself if you have any unspoken assumptions about how you have been doing things. You might consider revisiting them if they are not.
Try asking for help from another person if you're still stuck. You may be able to see things from a different perspective than you are and gain insight that can help you find a solution.
What are the key management skills?
Any business owner needs to be able to manage people, finances, resources and time. They include the ability to manage people, finances, resources, time, and space, as well as other factors.
When you need to manage people, set goals, lead teams, motivate them, solve problems, develop policies and procedures and manage change, management skills are essential.
There are so many managerial tasks!
How do you manage your employees effectively?
Effectively managing employees means making sure they are productive and happy.
It means setting clear expectations for them and keeping an eye on their performance.
Managers need to establish clear goals for their team and for themselves.
They must communicate clearly with their staff. They also need to make sure that they discipline and reward the best performers.
They must also keep track of the activities of their team. These include:
-
What was achieved?
-
What was the work involved?
-
Who did it?
-
How did it get done?
-
Why did it happen?
This information can be used for monitoring performance and evaluating results.
How does Six Sigma work?
Six Sigma uses statistical analyses to locate problems, measure them, analyze root cause, fix problems and learn from the experience.
The first step is to identify the problem.
The data is then analyzed and collected to identify trends.
The problem is then rectified.
Finally, the data are reanalyzed in order to determine if it has been resolved.
This cycle continues until the problem is solved.
What are some common management mistakes?
Sometimes managers make it harder for their employees than is necessary.
They may not assign enough responsibilities to staff members and provide them with inadequate support.
Managers often lack the communication skills necessary to motivate and guide their teams.
Some managers set unrealistic expectations for their staff.
Managers might try to solve every problem by themselves rather than delegating the responsibility.
What are management concepts, you ask?
Management concepts are the practices and principles managers use to manage people or resources. They cover topics such as job descriptions and performance evaluations, human resource policies, training programs, employee motivation, compens systems, organizational structure, among others.
Statistics
- UpCounsel accepts only the top 5 percent of lawyers on its site. (upcounsel.com)
- This field is expected to grow about 7% by 2028, a bit faster than the national average for job growth. (wgu.edu)
- The profession is expected to grow 7% by 2028, a bit faster than the national average. (wgu.edu)
- Hire the top business lawyers and save up to 60% on legal fees (upcounsel.com)
- The average salary for financial advisors in 2021 is around $60,000 per year, with the top 10% of the profession making more than $111,000 per year. (wgu.edu)
External Links
How To
How do I get my Six Sigma license?
Six Sigma is a quality control tool that improves processes and increases efficiency. It's a methodology that helps companies achieve consistent results from their operations. The name "Sigmas" comes from the Greek words "sigmas", meaning "six". Motorola created this process in 1986. Motorola recognized the need to standardize manufacturing processes in order to produce better products at a lower cost. There were many people doing the work and they had difficulty achieving consistency. To solve this problem, they decided to use statistical tools such as control charts and Pareto analysis. Then they would apply the techniques to all parts of the operation. So, after applying this technique, they would be able to make changes where there was room for improvement. When you are trying to obtain your Six Sigma certification, there are three steps. Finding out if the certification is available for you is the first step. Before you take any exams, you'll need to take some classes. You can then start taking the tests once you have completed those classes. You will want to remember everything you learned in the class. After that, you can take the test. You will be certified if you pass the test. Finally, your certifications will be added to your resume.