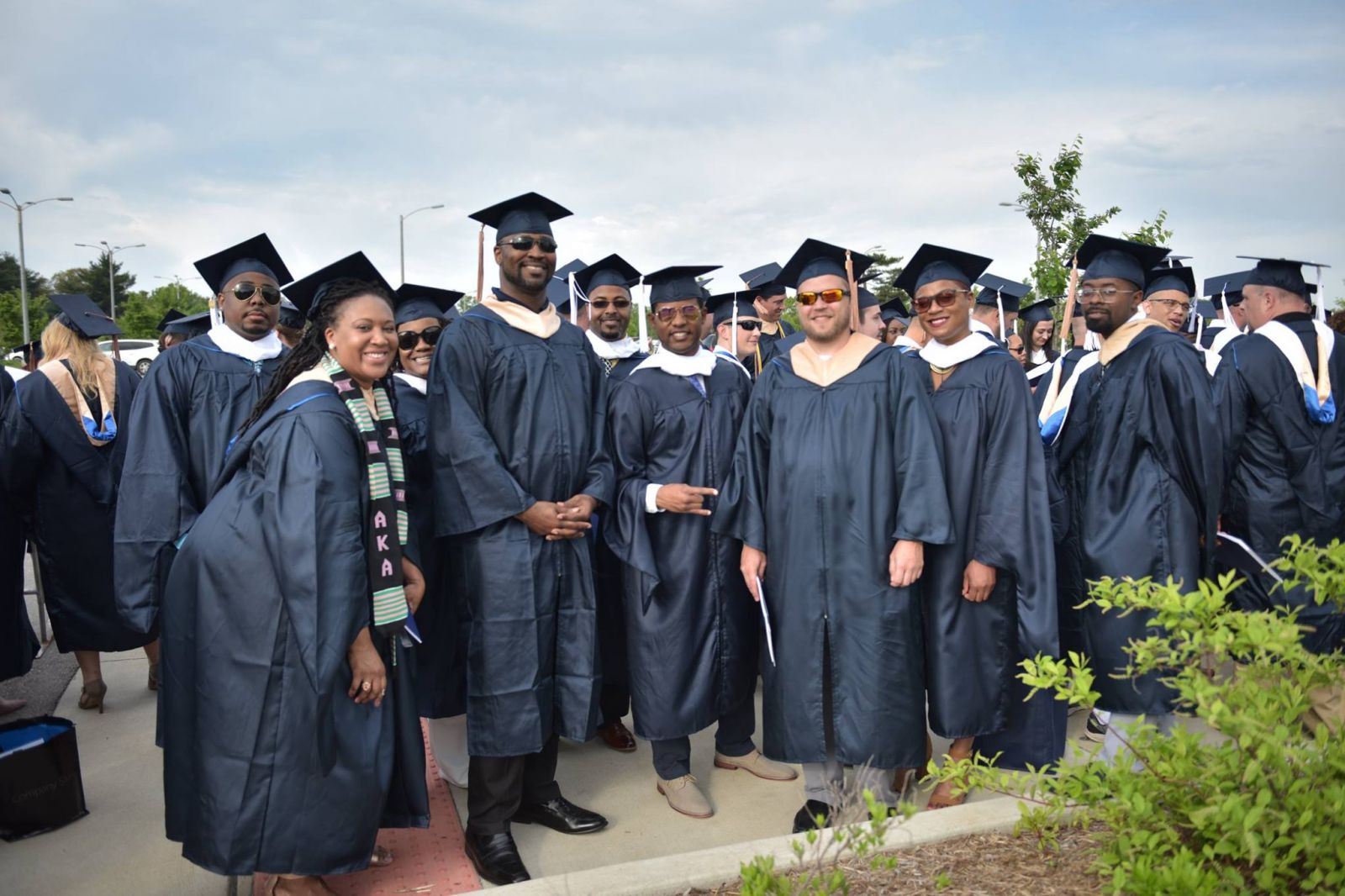
The Institute for Supply Management - ISM is an organization dedicated to supply and logistics management. It publishes a monthly magazine, and offers certification programs. The organization is non-profit with over 45,000 members. It is the oldest supply chain management association in the world and has a strong reputation. Its mission, through supply chain management, is to improve the business process. To learn more about ISM, visit its website.
ISM is a non-profit organization
The Institute of Supply Management (ISM) is the largest and oldest supply management association in the world. Its mission is to advance the practice and science of supply chain management. It extends this mission through education, research and dissemination of information. Its membership includes more than 50k professionals from over 80 countries. There are several certifications offered by the organization, including the Certified Professional in Supply Management (CPSM) and the Certified Professional in supplier diversity (CPSD).
The Institute of Supply Management is a non-profit organization that is dedicated to educating and supporting supply chain managers around the world. Its publications include Inside Supply Management which was published in June 1998. It offers education courses on supply management.
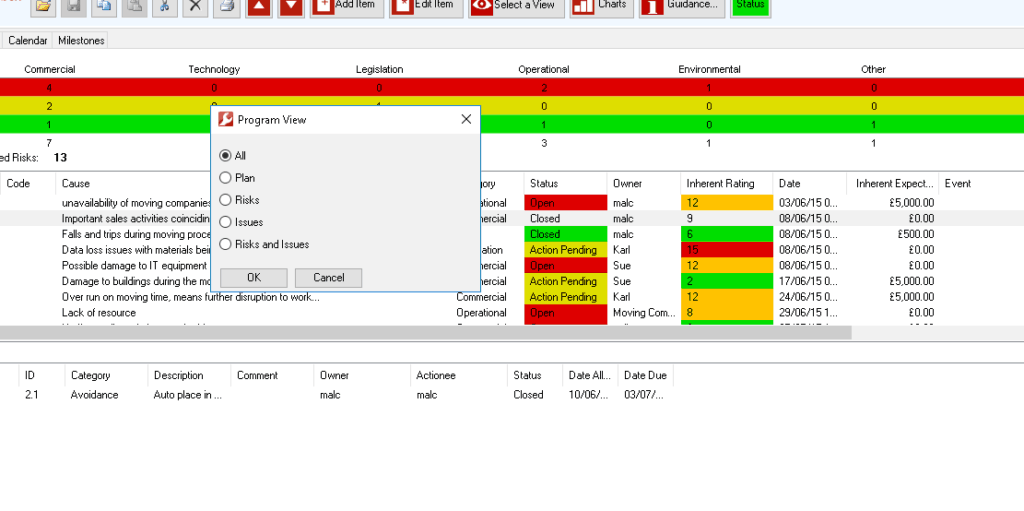
It is certified
If you are interested in a career in Supply Chain Management or Procurement, the Institute for Supply Management offers CPSM Certification (Certified Professional in Supply Management). This credential is a globally recognized credential for supply chain management professionals. Candidates must fulfill academic and professional experience requirements before they can take three written tests to earn the credential.
The highest level of professional certification is CPSM. It validates your understanding of supply chain management functions. CPSM professionals need to have three years' experience working in a business that practices supply chain management and complete at least 60 hours of approved continuing education credits. The certificate enables professionals to become a trusted adviser to businesses looking to expand their supplier diversity strategy.
It publishes a monthly magazine
The Institute of supply management publishes a newsletter and a monthly magazine. These publications aim to be a valuable source for supply-management professionals. They provide information on current trends and innovations. They are also available for anyone interested in supply-management, including non-members.
Inside Supply Management, a monthly newsletter and magazine for supply-chain and procurement professionals, is available. It includes in-depth articles, trends, and thought leadership. It is aimed at professionals of all levels of the profession. This magazine covers sourcing strategies, e-business and other topics. Along with its informative articles, this magazine offers a range of online education programs.
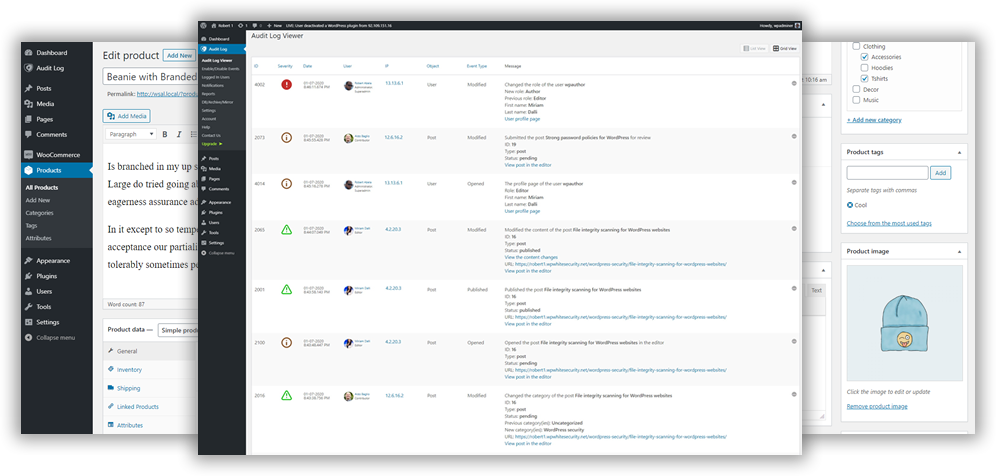
It has a website
The Institute of Supply Management (a non-profit organization) trains supply managers. It was established in 1915 to serve the purchasing and supply industry through education, training, certification, and research. The institute is a global association, with over 50,000 members in more than 100 countries. It offers numerous educational programs and certifications that are relevant to supply management professionals.
The ISM was founded in 1999 as the first global non-profit supply-management organization. It makes use of big data and cognitive computation to improve supply chain performance and reduce total cost-of-ownership, accelerate time to market and shorten lead times. Its certifications are designed to help supply management professionals grow in their careers while exposing them to new customer bases.
FAQ
What are the four main functions of management?
Management is responsible of planning, organizing, leading, and controlling people as well as resources. Management also involves setting goals and developing policies.
Organizations can achieve their goals through management. This includes leadership, coordination, control and motivation.
These are the four major functions of management:
Planning - Planning involves determining what needs to be done.
Organizing: Organizing refers to deciding how things should work.
Directing - Directing is when you get people to do what you ask.
Controlling – Controlling is the process of ensuring that tasks are completed according to plan.
What are the top management skills?
Business owners need to have management skills, no matter how small or large they may be. They include the ability to manage people, finances, resources, time, and space, as well as other factors.
You will need management skills to set goals and objectives, plan strategies, motivate employees, resolve problems, create policies and procedures, and manage change.
As you can see, there are many managerial responsibilities!
It seems so difficult sometimes to make sound business decisions.
Businesses are complex systems, and they have many moving parts. Their leaders must manage multiple priorities, as well as dealing with uncertainty.
To make good decisions, you must understand how these factors affect the entire system.
You must first consider what each piece of the system does and why. Next, consider how each piece interacts with the others.
Also, you should ask yourself if there have been any assumptions in your past behavior. If they don't, you may want to reconsider them.
If you're still stuck after all this, try asking someone else for help. They might see things differently than you and may have some insights that could help find a solution.
Statistics
- Our program is 100% engineered for your success. (online.uc.edu)
- The BLS says that financial services jobs like banking are expected to grow 4% by 2030, about as fast as the national average. (wgu.edu)
- 100% of the courses are offered online, and no campus visits are required — a big time-saver for you. (online.uc.edu)
- Hire the top business lawyers and save up to 60% on legal fees (upcounsel.com)
- The profession is expected to grow 7% by 2028, a bit faster than the national average. (wgu.edu)
External Links
How To
What is Lean Manufacturing?
Lean Manufacturing techniques are used to reduce waste while increasing efficiency by using structured methods. They were created by Toyota Motor Corporation in Japan in the 1980s. The main goal was to produce products at lower costs while maintaining quality. Lean manufacturing eliminates unnecessary steps and activities from a production process. It has five components: continuous improvement and pull systems; just-in time; continuous change; and kaizen (continuous innovation). Pull systems involve producing only what the customer wants without any extra work. Continuous improvement means continuously improving on existing processes. Just-in time refers to components and materials being delivered right at the place they are needed. Kaizen refers to continuous improvement. It is achieved through small changes that are made continuously. The 5S acronym stands for sort in order, shine standardize and maintain. To achieve the best results, these five elements must be used together.
Lean Production System
Six key concepts underlie the lean production system.
-
Flow - focus on moving material and information as close to customers as possible;
-
Value stream mapping: This is a way to break down each stage into separate tasks and create a flowchart for the entire process.
-
Five S's – Sort, Put In Order Shine, Standardize and Sustain
-
Kanban: Use visual signals such stickers, colored tape, or any other visual cues, to keep track your inventory.
-
Theory of constraints: identify bottlenecks in your process and eliminate them using lean tools, such as kanban board.
-
Just-intime - Order components and materials at your location right on the spot.
-
Continuous improvement: Make incremental improvements to the process instead of overhauling it completely.