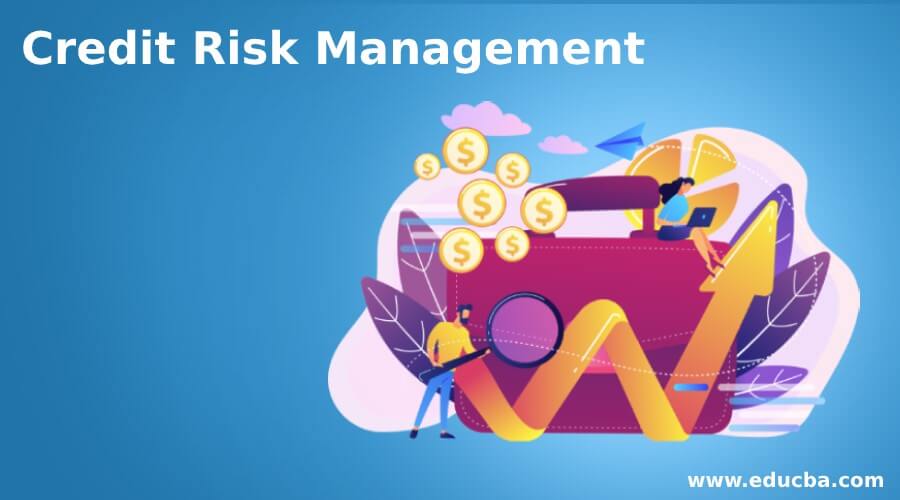
A bachelor's degree is required to move up in your career. A 120-credit program gives you in-depth knowledge of operations management and logistics. The program has been accredited by NEASC and covers topics like continuous improvement tools. U.S. News ranked this program highly and it is also available online.
Online supply chain management degree programs
You can advance your career by completing an online supply chain management degree program. These programs prepare you to tackle today's most difficult challenges by focusing on logistics and warehouse operations. Learn how to negotiate with suppliers and maximize warehouse efficiency. These programs are also flexible, so you can earn a degree part-time or full-time.
An online supply chain management degree can cost as little as $8,550 depending on the program that you choose. It is also important to consider where you live, as some colleges have higher tuition rates for students from out of state. Private scholarships are also available to finance your education. Technology costs are often included in tuition. A supply chain management degree program will typically cost between $36,000 and $64,000 for a full-time student.
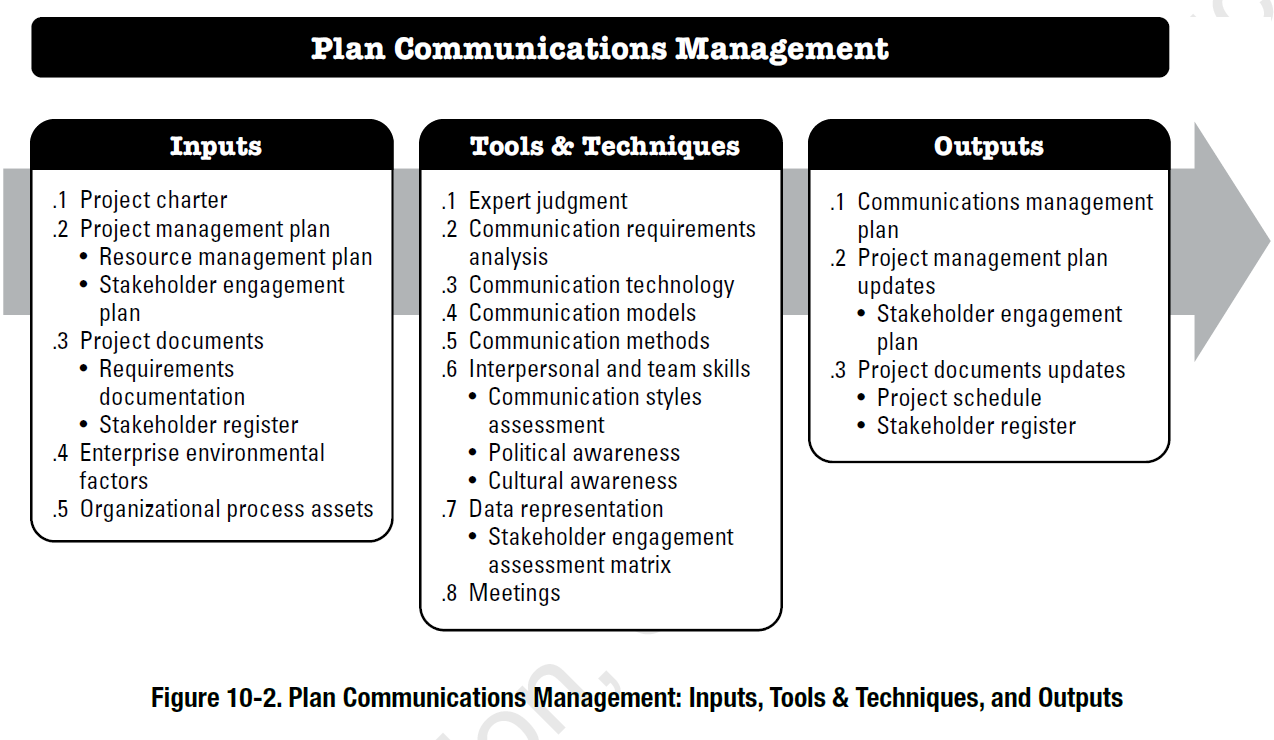
Degree programs in Supply Chain Management that are Accredited
Students can gain the necessary skills and knowledge to be successful in supply chain management by completing accredited degree programs. These online degrees are available in a wide range of subjects. Some degree programs include a capstone project, an internship, or study abroad. Although these programs do not have the same depth as conventional degrees, they are flexible.
A variety of skills are required for students who wish to work in supply chain management. These skills include communication, problem solving, and analytical skills. For this job, you will need to have a strong understanding of business systems and a strong business background.
Programs in supply chain management for distance learning
There are many institutions that offer online supply chain management degrees. Some schools are accredited by the Higher Learning Commission, while others are not. Online students receive the same support and resources that on-campus students. The best online degrees offer both online classes and classroom instruction.
An assortment of factors can affect the cost for an online degree. A key factor in determining whether or not a student resides in the state where the school is situated is whether they are eligible for financial aid. Some colleges charge higher tuition for out-of-state students, while others charge a flat rate for all students. Additionally, students should factor in technology fees. On average, students should budget between $36,000 and $64,000 for tuition and fees.
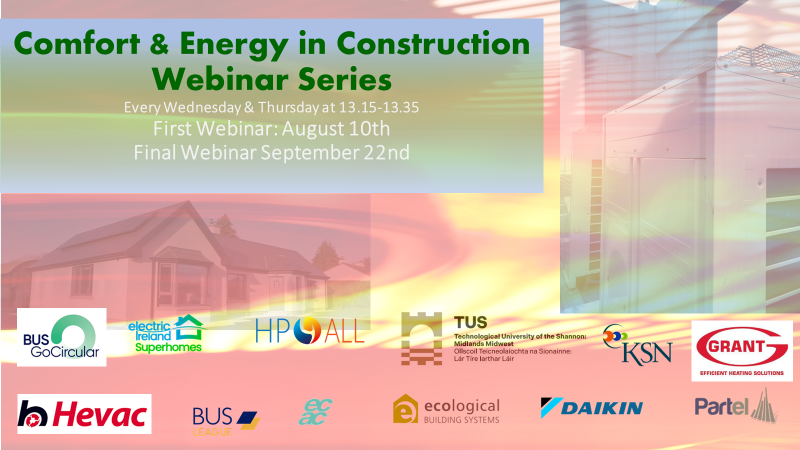
List of Supply Chain Management Degree Programs
The University of Arkansas maintains its pole position according to the most recent rankings of supply chain management degree programmes. It is currently ranked in the Top 3. The University of South Carolina and the University of Tennessee round out the Top 3 in the report. The top schools tend to be more competitive and expensive. In recent years, the focus of supply chain management has shifted to risk management and sustainability.
USC Marshall School of Business, another respected institution, offers flexible programs that can be completed either on campus or online. Other top-ranked schools are the Alliance Manchester Business School (Business School), Trinity Business School (Business School), and Politecnico di Milano School of Management. The University of Washington Foster School of Business also ranks among the top 10. These rankings are based upon a survey of more than 50k business leaders who have graduated at business schools all over the globe.
FAQ
What are some common mistakes managers make?
Managers sometimes make their own job harder than necessary.
They may not be able to delegate enough responsibility to staff or provide adequate support.
Managers often lack the communication skills necessary to motivate and guide their teams.
Managers sometimes set unrealistic expectations of their teams.
Managers might try to solve every problem by themselves rather than delegating the responsibility.
What does "project management" mean?
Management is the act of managing activities in order to complete a project.
These include planning the scope and identifying the needs, creating the budget, organizing the team, scheduling the work and monitoring progress. Finally, we close down the project.
What are the 3 basic management styles?
The three major management styles are authoritarian (left-faire), participative and laissez -faire. Each style has strengths and flaws. Which style do your prefer? Why?
Autoritarian - The leader sets direction and expects everyone else to follow it. This style is best when the organization has a large and stable workforce.
Laissez-faire – The leader gives each individual the freedom to make decisions for themselves. This approach works best in small, dynamic organizations.
Participative - The leader listens to ideas and suggestions from everyone. This is a great style for smaller organizations that value everyone.
How do you effectively manage employees?
The key to effective management of employees is ensuring their happiness and productivity.
It is important to set clear expectations about their behavior and keep track of their performance.
To do this successfully, managers need to set clear goals for themselves and for their teams.
They must communicate clearly with their staff. They also need to make sure that they discipline and reward the best performers.
They must also keep records of team activities. These include:
-
What was achieved?
-
How much work were you able to accomplish?
-
Who did it?
-
When it was done?
-
Why did it happen?
This information can be used for monitoring performance and evaluating results.
What is the difference between Six Sigma Six Sigma and TQM?
The key difference between the two quality management tools is that while six-sigma focuses its efforts on eliminating defects, total quality management (TQM), focuses more on improving processes and reducing cost.
Six Sigma stands for continuous improvement. This approach emphasizes eliminating defects through statistical methods like control charts, Pareto analysis, and p-charts.
This method aims to reduce variation in product production. This is accomplished by identifying the root cause of problems and fixing them.
Total quality management includes monitoring and measuring all aspects of an organization's performance. It also includes the training of employees to improve performance.
It is used to increase productivity.
What is a basic management tool used in decision-making?
The decision matrix is a powerful tool that managers can use to help them make decisions. It allows them to think through all possible options.
A decision matrix is a way of representing alternatives as rows and columns. This makes it easy for you to see how each option affects other options.
This example shows four options, each represented by the boxes on either side of the matrix. Each box represents an option. The top row depicts the current status quo, while the bottom row represents what would happen if no action was taken.
The effect of choosing Option 1 can be seen in column middle. It would increase sales by $2 million to 3 million in this instance.
The results of choosing Option 2 and 3 can be seen in the columns below. These positive changes can increase sales by $1 million or $500,000. They also have negative consequences. Option 2 can increase costs by $100 million, while Option 3 can reduce profits by $200,000.
The final column shows results of choosing Option 4. This results in a decrease of sales by $1,000,000
The best thing about a decision matrix is the fact that you don't have to remember which numbers go with what. The best thing about a decision matrix is that you can simply look at the cells, and immediately know whether one option is better or not.
This is because the matrix has done all the hard work. It's as easy as comparing numbers in the appropriate cells.
Here is an example how you might use the decision matrix in your company.
It is up to you to decide whether to spend more money on advertising. If you do this, you will be able to increase revenue by $5000 per month. But, you will also incur additional expenses of $10 thousand per month.
If you look at the cell that says "Advertising", you can see the number $15,000. Advertising is worth much more than the investment cost.
What is Kaizen and how can it help you?
Kaizen is a Japanese term for "continuous improvement." It encourages employees constantly to look for ways that they can improve their work environment.
Kaizen is built on the belief that everyone should be able do their jobs well.
Statistics
- Hire the top business lawyers and save up to 60% on legal fees (upcounsel.com)
- As of 2020, personal bankers or tellers make an average of $32,620 per year, according to the BLS. (wgu.edu)
- This field is expected to grow about 7% by 2028, a bit faster than the national average for job growth. (wgu.edu)
- Your choice in Step 5 may very likely be the same or similar to the alternative you placed at the top of your list at the end of Step 4. (umassd.edu)
- The BLS says that financial services jobs like banking are expected to grow 4% by 2030, about as fast as the national average. (wgu.edu)
External Links
How To
How do I do the Kaizen Method?
Kaizen means continuous improvement. This Japanese term refers to the Japanese philosophy of continuous improvement that emphasizes incremental improvements and constant improvement. This is a collaborative process in which people work together to improve their processes continually.
Kaizen is one method that Lean Manufacturing uses to its greatest advantage. In this concept, employees who are responsible for the production line must identify problems that exist during the manufacturing process and try to solve them before they become big issues. This improves the quality of products, while reducing the cost.
The main idea behind kaizen is to make every worker aware of what happens around him/her. Correct any errors immediately to avoid future problems. Report any problem you see at work to your manager.
Kaizen is based on a few principles. The end product is always our starting point and we work toward the beginning. We can improve the factory by first fixing the machines that make it. First, we fix machines that produce components. Next, we fix machines that produce raw material. And finally, we fix the workers who work directly with those machines.
This is known as "kaizen", because it emphasizes improving each step. Once the factory is fixed, we return to the original site and work our way back until we get there.
Before you can implement kaizen into your business, it is necessary to learn how to measure its effectiveness. There are many ways to tell if kaizen is effective. One way is to examine the amount of defects on the final products. Another way is to check how much productivity has grown since kaizen was implemented.
You can also find out if kaizen works by asking yourself why you decided to implement it. Did you do it because it was legal or to save money? You really believed it would make you successful?
Let's say you answered yes or all of these questions. Congratulations! You are now ready to begin kaizen.