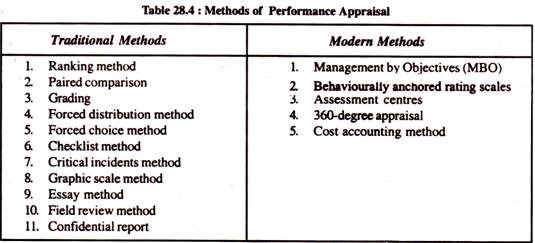
What are the different types of jobs in critical infrastructure? These are jobs in the energy and water industries. These jobs are important for a country's economic stability and national security. They may require written documentation. These are just a few examples of such jobs. This type of work requires special training.
Examples of critical infrastructure workers
Protection of communities is possible only with the help of critical infrastructure workers. These individuals are a critical component of public safety, health and economic security. These workers can be identified and protected to promote resilience in communities and maintain essential functions. These are some examples of critical infrastructure workers, and what their roles are. They provide essential services to communities and are an integral part of society.
CISA, Cybersecurity and Infrastructure Security Agency, has produced a list ECIW. CISA has not yet assigned any classifications to these workers, even though this list is considered the most comprehensive and complete national definition. The agency recognizes that some workers may work across multiple industries. The agency recognizes that critical infrastructure workers may be classified in construction or information technology.
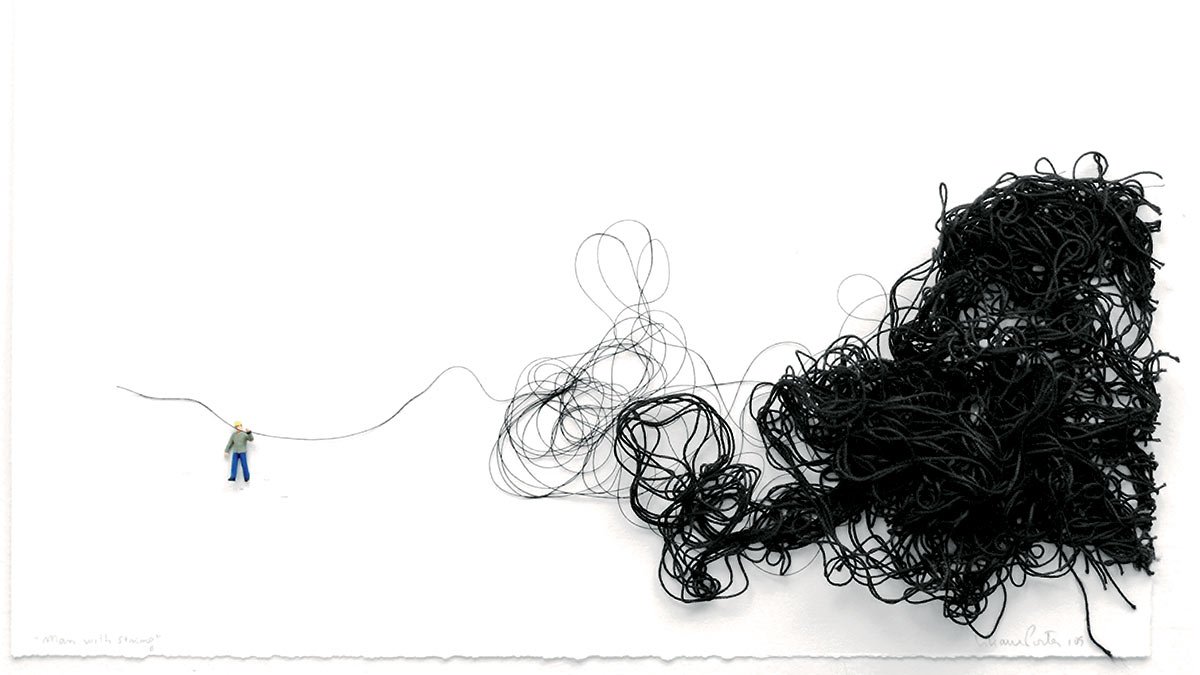
Many industries contribute to the provision of critical infrastructure and provide essential jobs. Transport and logistics workers ship and distribute products. IT workers, media workers, and emergency responders are all examples. Other essential sectors include those who provide legal and accounting services, and building trades workers.
You can work in the energy sector
Work in the energy sector is growing faster than most other sectors of the economy. According to the 2020 U.S. Energy and Employment Report, released by the National Association of State Energy Officials, the energy sector employed nearly seven million Americans in 2019. The growth was driven by fuel production, electric power generation, motor vehicles, and transmission, distribution, and storage, which now account for nearly three percent of the nation's total employment.
The United States has an energy infrastructure that is the heart of 21st-century economic life. Without a secure and reliable supply of energy, our economy cannot operate. This is why Presidential Policy Directive 21 designated the Energy Sector as one of the most critical infrastructure sectors. Around 80 percent of the energy infrastructure is privately owned and supplies electricity to homes and businesses.
Work in the water sector
Although the water industry plays an important role in the economy, there are also challenges. Many water workers will retire over the next few years as the system ages. Many water workers are skilled in technical maintenance, but they also have the ability to perform administrative, financial, or management tasks. Although water workers make up only one to two percent of the entire workforce, they are crucial to the economy and society.

Water companies must be prepared for the inevitable disruptions that may occur due to cyberattacks. With increasing automation in the water sector, malicious cyber activity is possible. In one recent incident, a hacker nearly managed to increase the concentration of a caustic agent in drinking water by breaching a monitoring system used by the water utility to comply with regulations. Unfortunately, most utilities don't invest in cybersecurity to implement new technology or systems.
FAQ
What are some of the common mistakes made by managers?
Sometimes managers make their job harder than they need to.
They may not be able to delegate enough responsibility to staff or provide adequate support.
In addition, many managers lack the communication skills required to motivate and lead their teams.
Managers sometimes set unrealistic expectations of their teams.
Managers may attempt to solve all problems themselves, rather than delegating it to others.
What is the difference between a project and a program?
A program is permanent, whereas a project is temporary.
A project typically has a defined goal and deadline.
This is often done by a group of people who report to one another.
A program often has a set goals and objectives.
It is often implemented by one person.
What are the steps involved in making a decision in management?
Managers face complex and multifaceted decision-making challenges. It involves many factors, including but not limited to analysis, strategy, planning, implementation, measurement, evaluation, feedback, etc.
Remember that people are humans just like you, and will make mistakes. This is the key to managing them. As such, there is always room for improvement, especially if you're willing to put forth the effort to improve yourself first.
This video shows you how management makes decisions. We'll discuss the different types and reasons they are important. Managers should also know how to navigate them. Here are some topics you'll be learning about:
Statistics
- Hire the top business lawyers and save up to 60% on legal fees (upcounsel.com)
- Your choice in Step 5 may very likely be the same or similar to the alternative you placed at the top of your list at the end of Step 4. (umassd.edu)
- The BLS says that financial services jobs like banking are expected to grow 4% by 2030, about as fast as the national average. (wgu.edu)
- This field is expected to grow about 7% by 2028, a bit faster than the national average for job growth. (wgu.edu)
- As of 2020, personal bankers or tellers make an average of $32,620 per year, according to the BLS. (wgu.edu)
External Links
How To
How is Lean Manufacturing done?
Lean Manufacturing techniques are used to reduce waste while increasing efficiency by using structured methods. They were created by Toyota Motor Corporation in Japan in the 1980s. The primary goal was to make products with lower costs and maintain high quality. Lean manufacturing seeks to eliminate unnecessary steps and activities in the production process. It is composed of five fundamental elements: continuous improvement; pull systems, continuous improvements, just-in–time, kaizen, continuous change, and 5S. The production of only what the customer needs without extra work is called pull systems. Continuous improvement refers to continuously improving existing processes. Just-in–time refers when components or materials are delivered immediately to their intended destination. Kaizen stands for continuous improvement. Kaizen can be described as a process of making small improvements continuously. Five-S stands for sort. It is also the acronym for shine, standardize (standardize), and sustain. To achieve the best results, these five elements must be used together.
Lean Production System
The lean production system is based on six key concepts:
-
Flow is about moving material and information as near as customers can.
-
Value stream mapping - break down each stage of a process into discrete tasks and create a flowchart of the entire process;
-
Five S's – Sort, Put In Order Shine, Standardize and Sustain
-
Kanban - visual cues such as stickers or colored tape can be used to track inventory.
-
Theory of constraints: Identify bottlenecks and use lean tools such as kanban boards to eliminate them.
-
Just-in-time delivery - Deliver components and materials right to your point of use.
-
Continuous improvement - make incremental improvements to the process rather than overhauling it all at once.