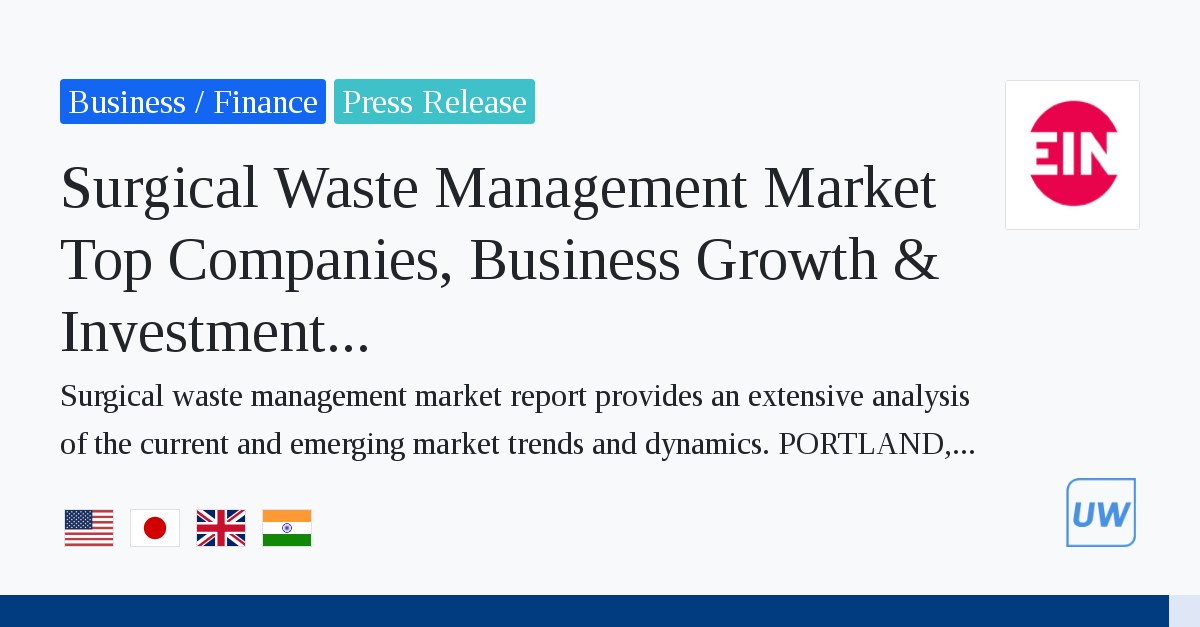
There are four major management perspectives. These perspectives are Theory, Function, Historical Development, and Future Trends. This article will cover each of these perspectives. Each perspective comes with its own advantages and disadvantages. It is important to know the differences between each viewpoint. This will allow you to pick the one that best suits you and your preferences. Here are some examples from management perspectives.
Theories of Management
The theories of management can help you determine the right management strategy for your organization. While each theory focuses on different aspects of organization behavior, they all have a common theme: the management needs. A combination of different theories can yield better results. While there is no one right answer, they all work well for some organizations. In fact, many modern organizations employ a mixture of theories, leading to more flexible organizational structures.
The theories of management can be applied in many settings, such as project management or general management. In project management, they are condensed bits of knowledge that make it possible for novices and experts to do the same thing. These techniques are most effective when they are applied in a small project environment, where theoretical issues can be addressed without imposing additional penalties. They can cause serious damage to performance and create problems that could be avoided by better management.
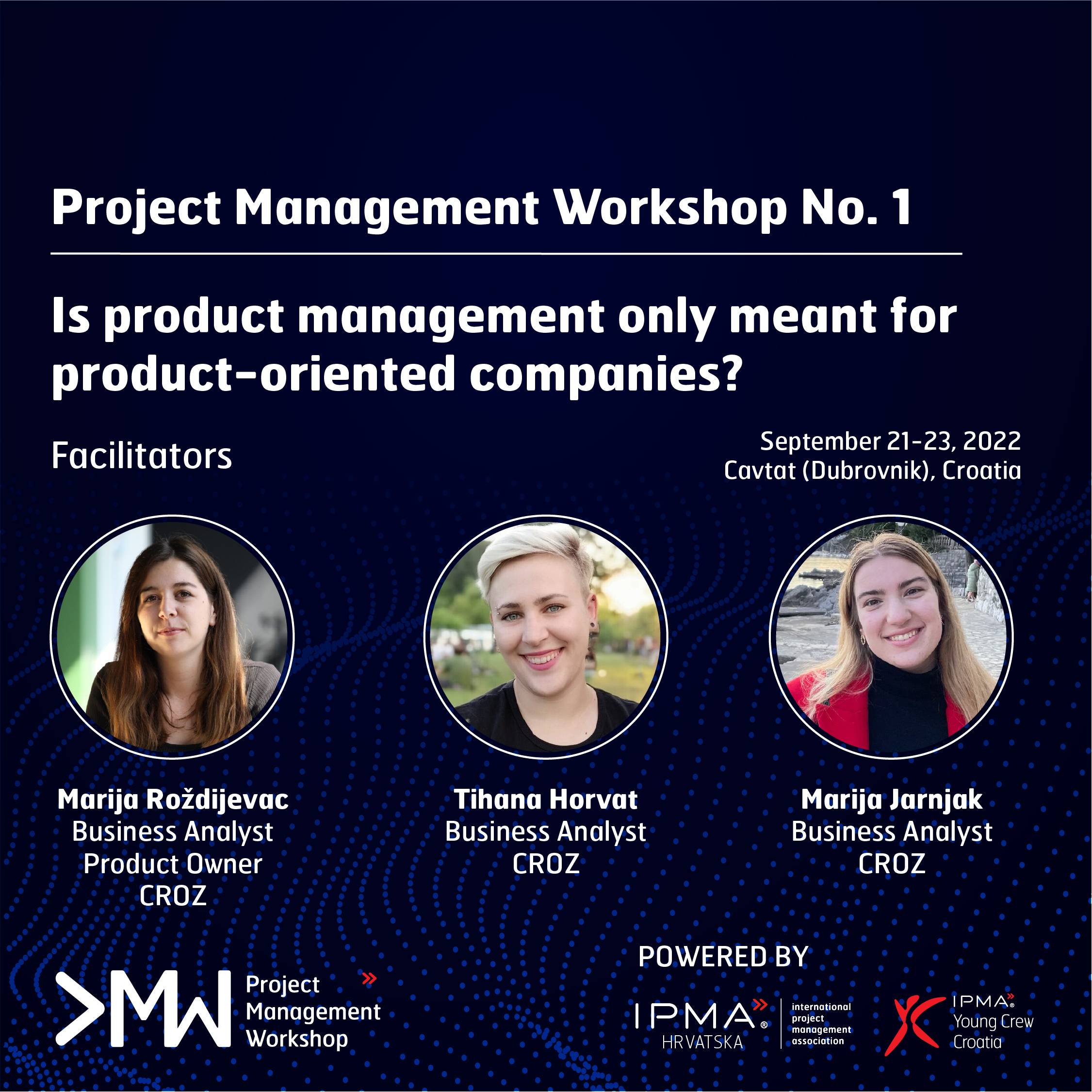
Management functions
The functions of management are important to the success of an organisation. These include planning, identifying the tasks, monitoring and correcting any problems. Management plays a significant role in an organization, particularly in meeting goals related to profit and market share. Managers must make decisions, set goals, implement strategies and track the progress of various parts of an organization.
Planning is the first stage of the management process. This involves setting goals and defining the purpose. It requires analytical skills, a good understanding of the past and current trends, and the ability to create and implement future plans. An organisation can achieve its objectives if it performs these functions well.
Historical development
Management has changed over the years, with new theories placing more emphasis on human factors. One prominent example of this development is Douglas McGregor's "Theory Y." This development also changed the traditional view of executives, which saw them no longer as masters of an organization but more like coaches. Organizational theorists began exploring the concept of emotional intelligence, the human element in managing, and the emphasis was completely changed.
The Industrial Revolution sparked intense debate about management theory. This was a turning point in the history of management. Six major management theories emerged from the resulting changes. Each of these theories focuses on different aspects of management.
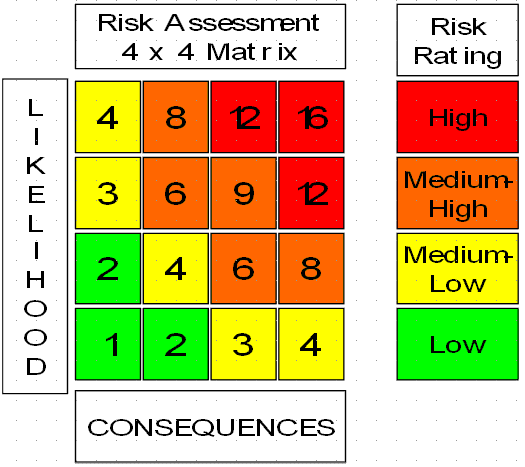
Future trends
A series of trends are shaping the future of management. One of these trends concerns the changing role that managers play. Managers need to be flexible and agile. Flexibility is becoming more mainstream in the UK. Flexible working is expected to become the norm in five years by more than half of UK managers. Half believe their direct reports work more flexiblely than they did five years ago.
One trend that is changing the management industry is the growing importance of working relationships. More than half of managers recognise this as a future trend and believe that they are more important now than five years ago. This trend is being supported by the rise of flexible working environments. Due to the economic crisis, some people have had to pay more attention and build trust with their friends. These new trends can help companies attract, develop and retain employees.
FAQ
What is Six Sigma?
It is a way to improve quality that places emphasis on customer service and continuous learning. The goal is to eradicate defects through statistical techniques.
Motorola developed Six Sigma in 1986 to help improve its manufacturing processes.
The idea spread quickly in the industry. Today many organizations use six-sigma techniques to improve product design.
What's the difference between Six Sigma and TQM?
The key difference between the two quality management tools is that while six-sigma focuses its efforts on eliminating defects, total quality management (TQM), focuses more on improving processes and reducing cost.
Six Sigma is a methodology for continuous improvement. This approach emphasizes eliminating defects through statistical methods like control charts, Pareto analysis, and p-charts.
This method aims to reduce variation in product production. This is achieved by identifying and addressing the root causes of problems.
Total quality management includes monitoring and measuring all aspects of an organization's performance. It also includes the training of employees to improve performance.
It is used to increase productivity.
How do you define Six Sigma?
Six Sigma is well-known to those who have worked in operations research and statistics. Anyone involved in business can benefit.
This requires a lot of dedication, so only people with great leadership skills can make the effort to implement it.
What are management principles?
Management Concepts are the management principles and practices that managers use in managing people and resources. They include such topics as human resource policies, job descriptions, performance evaluations, training programs, employee motivation, compensation systems, organizational structure, and many others.
How to manage employees effectively?
Effectively managing employees requires that you ensure their happiness and productivity.
It also means having clear expectations of their behavior and keeping track of their performance.
Managers must be clear about their goals and those of their teams in order to succeed.
They need to communicate clearly and openly with staff members. They need to communicate clearly with their staff.
They should also keep records of all activities within their team. These include:
-
What did we accomplish?
-
How much work did you put in?
-
Who did it and why?
-
It was done!
-
Why was it done?
This information can be used to monitor performance and evaluate results.
Statistics
- As of 2020, personal bankers or tellers make an average of $32,620 per year, according to the BLS. (wgu.edu)
- UpCounsel accepts only the top 5 percent of lawyers on its site. (upcounsel.com)
- The BLS says that financial services jobs like banking are expected to grow 4% by 2030, about as fast as the national average. (wgu.edu)
- The average salary for financial advisors in 2021 is around $60,000 per year, with the top 10% of the profession making more than $111,000 per year. (wgu.edu)
- The profession is expected to grow 7% by 2028, a bit faster than the national average. (wgu.edu)
External Links
How To
How can Lean Manufacturing be done?
Lean Manufacturing techniques are used to reduce waste while increasing efficiency by using structured methods. These processes were created by Toyota Motor Corporation, Japan in the 1980s. The main goal was to produce products at lower costs while maintaining quality. Lean manufacturing emphasizes removing unnecessary steps from the production process. It is made up of five elements: continuous improvement, continuous improvement, just in-time, continuous change, and 5S. It is a system that produces only the product the customer requests without additional work. Continuous improvement is constantly improving upon existing processes. Just-intime refers the time components and materials arrive at the exact place where they are needed. Kaizen stands for continuous improvement. Kaizen can be described as a process of making small improvements continuously. Last but not least, 5S is for sort. These five elements can be combined to achieve the best possible results.
Lean Production System
The lean production system is based on six key concepts:
-
Flow is about moving material and information as near as customers can.
-
Value stream mapping is the ability to divide a process into smaller tasks, and then create a flowchart that shows the entire process.
-
Five S's: Sort, Shine Standardize, Sustain, Set In Order, Shine and Shine
-
Kanban - use visual signals such as colored tape, stickers, or other visual cues to keep track of inventory;
-
Theory of constraints - identify bottlenecks during the process and eliminate them with lean tools like Kanban boards.
-
Just-in Time - Send components and material directly to the point-of-use;
-
Continuous improvement - incremental improvements are made to the process, not a complete overhaul.