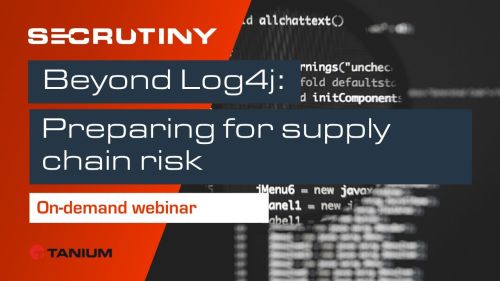
The Illinois State University Construction Management degree programs are a great option for anyone interested in a career working in construction management. This school is accredited by the Associated Schools of Construction. The program provides a hands-on approach to construction management and prepares students for the workforce. You will learn about the program's curriculum, job outlook, and GPA requirements. Online enrollment is also possible. Be aware of the requirements before applying.
Associated Schools of Construction
The region III student competition was held in Downers Grove (Illinois) on October 18-21. The second-placed team was led by Caleb Jacob. Joel Jimenez. Jose Quiroz. Russell Smallwood. Adam Wenberg. The Misericordia Bakery retail shop in Chicago was the project that the team completed. Walsh Construction Company sponsored the project.
By participating in a regional contest, students were able get to work on real-world projects. They were required to attend a prebid meeting, where they had thirteen hours to prepare the bid proposal. The team submitted the bid proposal by 8 p.m. on the same day. On Friday, October 22, they presented the proposal to Pepper Construction, who was pleased with the results. It required that team members have an understanding of plans, problem-solving skills and communication skills.
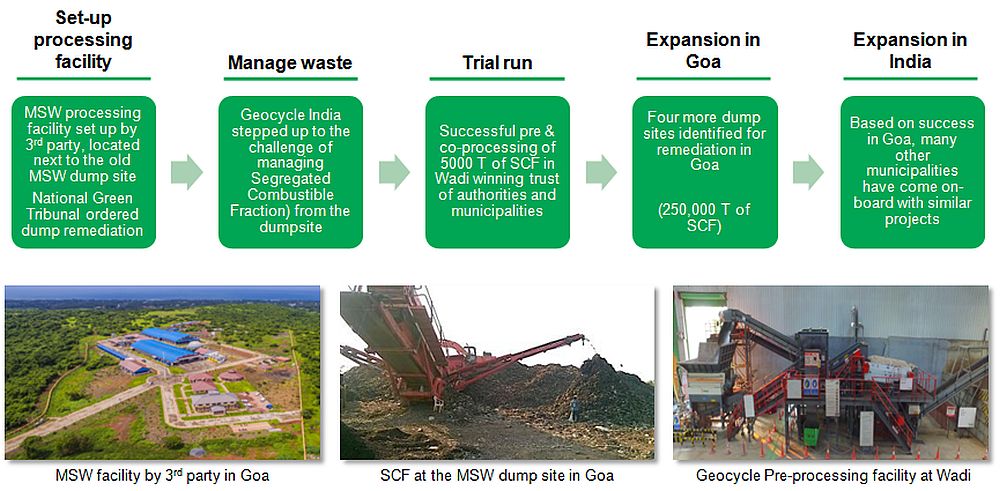
Curriculum
The Masters program at Illinois State University is designed to help those who are interested in a career as a construction manager. This program prepares students to take on leadership roles in the construction industry by combining technical knowledge and managerial skills. This program provides a wide range of opportunities for students to get practical experience in the field. The program is focused on business and management concepts. Students also learn how to care for the environment. An internship is part of this course.
The Curriculum for Illinois State University’s construction management program combines courses in business, communications, and engineering. It also contains courses in applied science, mathematics, and physics. The American Council for Construction Education has granted accreditation to the program. It is therefore open to the general public. It is also geared towards the needs of the construction sector. It will allow you to excel in your job as a professional in construction.
There are many job opportunities
Illinois State University's construction management program offers 182 majors and 40-50 graduates every year. It is a competitive program that attracts national and local construction contractors as well as home builders who are looking to hire people with solid track records. The program is accredited by the American Council on Construction Education, and is a part of the university's Sustainable and Renewable Energy programs. The program's annual career fair brings together both students and employers in order to assist graduates in finding employment in the building industry.
A student who completes the program could find a job in project management or construction management. The construction management field is expanding and managers must be able to do their job well. Construction managers are required to manage projects and oversee subcontractors. They also need to ensure that the construction process runs smoothly. The program offers numerous job opportunities for graduates, including for engineers, architects, and construction supervisors.
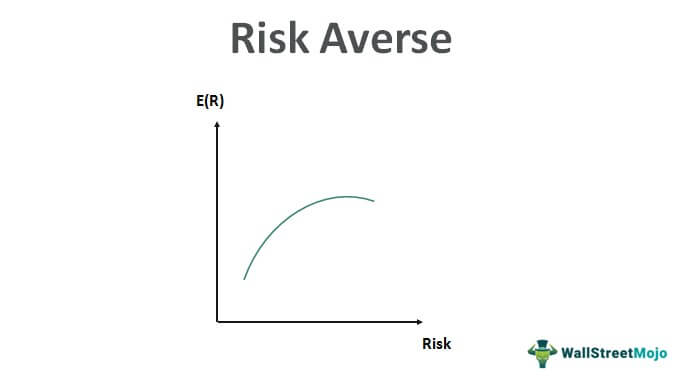
Admissions requires a GPA
In order to be considered for admission, you must have at least a 2.0 GPA in all college coursework. In addition, you must have a good academic record from your previous institution. Higher GPAs are required for most majors. Additional information may be required to prove your eligibility for a new degree. Learn more about Illinois State University's admission requirements.
If you have completed at minimum 12 hours of college work, you might be eligible for a new start. You must have completed at most 80 credits of construction-related coursework at a recognized post-secondary institution. Once you meet these requirements you can apply to the program. The GPA requirement for Illinois State University's construction management program is dependent on your academic record.
FAQ
How can we create a successful company culture?
A positive company culture creates a sense of belonging and respect in its people.
It's built on three fundamental principles:
-
Everybody has something of value to share
-
People are treated fairly
-
Individuals and groups can have mutual respect
These values are evident in the way that people act. For example, they will treat others with courtesy and consideration.
They will respect the opinions of others.
These people will inspire others to share thoughts and feelings.
The company culture promotes collaboration and open communication.
People feel safe to voice their opinions without fear of reprisal.
They are aware that mistakes can be accepted if they are treated honestly.
Finally, the company culture encourages honesty as well as integrity.
Everybody knows they have to tell the truth.
Everyone understands there are rules that they must follow.
People don't expect special treatment or favors.
Why is Six Sigma so popular?
Six Sigma is easy and can deliver significant results. It can also be used to help companies identify and focus on the most important aspects of their business.
What is the difference in a project and program?
A project is temporary while a programme is permanent.
Projects usually have a goal and a deadline.
This is often done by a group of people who report to one another.
A program will usually have a set number of goals and objectives.
It is often implemented by one person.
What is TQM?
When manufacturing companies realized that price was not enough to compete, the industrial revolution brought about the quality movement. If they wanted to stay competitive, they needed to improve their quality and efficiency.
To address this need for improvement management created Total Quality Management (TQM) which aimed to improve all aspects of an organization's performance. It included continual improvement processes, employee involvement, customer satisfaction, and customer satisfaction.
What are the 5 management processes?
Planning, execution, monitoring and review are the five stages of any business.
Setting goals for the future is part of planning. It includes defining what you want to achieve and how you plan to do it.
Execution is when you actually execute the plans. These plans must be adhered to by everyone.
Monitoring is the act of monitoring your progress towards achieving your targets. Regular reviews of performance against budgets and targets should be part of this process.
Every year, there are reviews. They give you an opportunity to review the year and assess how it went. If not, it is possible to make improvements for next year.
Evaluation takes place after the annual review. It helps you identify the successes and failures. It provides feedback about how people perform.
What are the main management skills?
No matter if they are running a local business or an international one, management skills are vital. These include the ability and willingness to manage people, finances as well resources, time and space.
Management Skills are also needed when you're setting goals and objectives, planning strategies, leading teams, motivating employees, resolving problems, creating policies and procedures, and managing change.
As you can see, there's no end to the list of managerial duties!
What is Six Sigma?
It's a method for quality improvement that focuses on customer service as well as continuous learning. This is an approach to quality improvement that uses statistical techniques to eliminate defects.
Motorola invented Six Sigma in 1986 as part its efforts to improve manufacturing.
The idea spread quickly throughout the industry, and today, many organizations are using six sigma methods to improve product design, production, delivery, and customer service.
Statistics
- The BLS says that financial services jobs like banking are expected to grow 4% by 2030, about as fast as the national average. (wgu.edu)
- The profession is expected to grow 7% by 2028, a bit faster than the national average. (wgu.edu)
- UpCounsel accepts only the top 5 percent of lawyers on its site. (upcounsel.com)
- As of 2020, personal bankers or tellers make an average of $32,620 per year, according to the BLS. (wgu.edu)
- 100% of the courses are offered online, and no campus visits are required — a big time-saver for you. (online.uc.edu)
External Links
How To
How can you use the Kaizen method?
Kaizen means continuous improvement. The Japanese philosophy emphasizes small, incremental improvements to achieve continuous improvement. This term was created by Toyota Motor Corporation in 1950. It's where people work together in order to improve their processes constantly.
Kaizen is one method that Lean Manufacturing uses to its greatest advantage. The concept involves employees responsible for manufacturing identifying problems and trying to fix them before they become serious issues. This will increase the quality and decrease the cost of the products.
Kaizen is a way to raise awareness about what's happening around you. To prevent problems from happening, any problem should be addressed immediately. It is important that employees report any problems they see while on the job to their managers.
Kaizen has a set of basic principles that we all follow. The end product is always our starting point and we work toward the beginning. We can improve the factory by first fixing the machines that make it. Next, we fix the machines which produce components. And finally, we fix the workers who work directly with those machines.
This approach is called 'kaizen' because it focuses on improving everything steps by step. Once the factory is fixed, we return to the original site and work our way back until we get there.
Before you can implement kaizen into your business, it is necessary to learn how to measure its effectiveness. There are several ways that you can tell if your kaizen system is working. One method is to inspect the finished products for defects. Another way to find out how productive your company has been since you implemented kaizen is to measure the increase in productivity.
To determine if kaizen is effective, you should ask yourself why you chose to implement kaizen. Did you do it because it was legal or to save money? It was a way to save money or help you succeed.
Let's say you answered yes or all of these questions. Congratulations! You're ready to start kaizen.