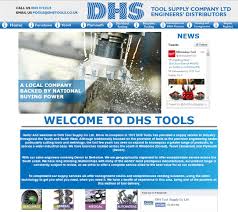
Regularly published articles on supply chain management appear in a number of journals. The number and type of articles published will depend on the journal. Most articles are about SMEs and high-demand products. Some articles explore the agency theory, and its effects on supply chain management. Next, we will provide an overview on articles published in various journals.
Trends in articles on supply chain management
Businesses are dependent on supply chains for their survival. They must function smoothly, regardless of whether they are online or offline. The disruption of a supply chain can lead to disruptions in the business' entire operations, including a COVID-19-related pandemic and a labor shortfall. However, supply chain statistics and trends can help businesses prepare for any potential changes.
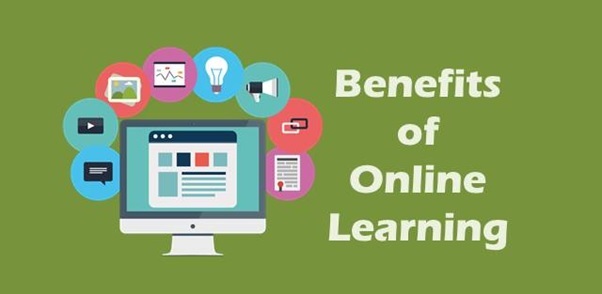
Supply chains are evolving as a result of several factors, including customer expectations and technological advances. Companies must be capable of managing multiple customer channels and fulfilment models as well as payment options and physical systems. To optimize their supply chain, some companies are turning to artificial Intelligence (AI). This technology is expected to not only save money, but also speed up the process.
Assocation of researchers who are interested in articles about supply chain management
The Association of Affiliated Researchers in Articles on Supply Chain Management produces a ranking of supply chains management research output. Its basis is the number of publications in previous five years. Submissions are evaluated on their relevance to supply chain management research topics, methodological rigor, and significant advancement of knowledge.
AAF publishes many reports on a wide range topics. These reports provide insights into the trends in the supply chain as well as the procurement industry. Topics covered include supply chain planning, forecasting, big data, inventory management, and sales and operations planning.
The majority of articles concern SMEs.
Although most articles about supply chain management are focused on large corporations with global operations, there are some articles that focus on the role and responsibilities of SMEs. Zowada (2011) states that the key to linking is the ability for SMEs to be adaptable and flexible, which are essential factors in creating a competitive advantage.
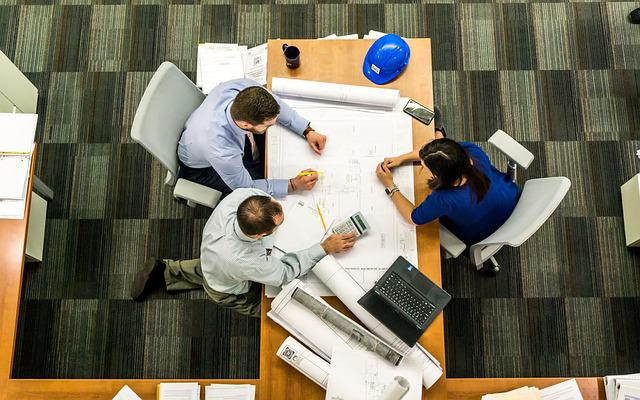
SME’s make up a significant part of all economies and societies. They are now facing increasing threats to their growth. Luckily, governments can take lessons from their success stories and devise new programs to help SMEs thrive in the modern age.
FAQ
What does it mean to say "project management"
We mean managing the activities involved in carrying out a project.
We help you define the scope of your project, identify the requirements, prepare the budget, organize the team, plan the work, monitor progress and evaluate the results before closing down the project.
How can we create a successful company culture?
A company culture that values and respects its employees is a successful one.
It is based on three principles:
-
Everybody has something to offer.
-
People are treated fairly
-
Respect is shared between individuals and groups
These values reflect in how people behave. They will treat others with respect and kindness.
They will respect other people's opinions.
These people will inspire others to share thoughts and feelings.
The company culture promotes collaboration and open communication.
People feel safe to voice their opinions without fear of reprisal.
They know mistakes will be accepted as long as they are dealt with honestly.
Finally, the company culture encourages honesty as well as integrity.
Everybody knows they have to tell the truth.
Everyone understands there are rules that they must follow.
And no one expects special treatment or favors.
What's the difference between Six Sigma and TQM?
The major difference between the two tools for quality management is that six Sigma focuses on eliminating defect while total quality control (TQM), on improving processes and decreasing costs.
Six Sigma can be described as a strategy for continuous improvement. This approach emphasizes eliminating defects through statistical methods like control charts, Pareto analysis, and p-charts.
This method has the goal to reduce variation of product output. This is done by identifying root causes and rectifying them.
Total Quality Management involves monitoring and measuring every aspect of the organization. It also includes the training of employees to improve performance.
It is used to increase productivity.
What are the top management skills?
No matter if they are running a local business or an international one, management skills are vital. These skills include the ability manage people, finances and resources as well as other factors.
When you need to manage people, set goals, lead teams, motivate them, solve problems, develop policies and procedures and manage change, management skills are essential.
As you can see, there are many managerial responsibilities!
What role does a manager have in a company's success?
Different industries have different roles for managers.
A manager generally manages the day to-day operations in a company.
He/she ensures that the company meets its financial obligations and produces goods or services that customers want.
He/she ensures employees adhere to all regulations and quality standards.
He/she plans new products and services and oversees marketing campaigns.
Statistics
- The profession is expected to grow 7% by 2028, a bit faster than the national average. (wgu.edu)
- The average salary for financial advisors in 2021 is around $60,000 per year, with the top 10% of the profession making more than $111,000 per year. (wgu.edu)
- The BLS says that financial services jobs like banking are expected to grow 4% by 2030, about as fast as the national average. (wgu.edu)
- Your choice in Step 5 may very likely be the same or similar to the alternative you placed at the top of your list at the end of Step 4. (umassd.edu)
- As of 2020, personal bankers or tellers make an average of $32,620 per year, according to the BLS. (wgu.edu)
External Links
How To
What is Lean Manufacturing?
Lean Manufacturing processes are used to reduce waste and improve efficiency through structured methods. They were created by Toyota Motor Corporation in Japan in the 1980s. The aim was to produce better quality products at lower costs. Lean manufacturing emphasizes removing unnecessary steps from the production process. It consists of five basic elements: pull systems, continuous improvement, just-in-time, kaizen (continuous change), and 5S. Pull systems allow customers to get exactly what they want without having to do extra work. Continuous improvement is the continuous improvement of existing processes. Just-in-time refers to when components and materials are delivered directly to the point where they are needed. Kaizen means continuous improvement. Kaizen involves making small changes and improving continuously. Finally, 5S stands for sort, set in order, shine, standardize, and sustain. These five elements can be combined to achieve the best possible results.
Lean Production System
Six key concepts form the foundation of the lean production system:
-
Flow - The focus is on moving information and material as close as possible to customers.
-
Value stream mapping - Break down each stage in a process into distinct tasks and create an overview of the whole process.
-
Five S's – Sort, Put In Order Shine, Standardize and Sustain
-
Kanban: Use visual signals such stickers, colored tape, or any other visual cues, to keep track your inventory.
-
Theory of Constraints - Identify bottlenecks in the process, and eliminate them using lean tools such kanban boards.
-
Just-in-time - deliver components and materials directly to the point of use;
-
Continuous improvement - incremental improvements are made to the process, not a complete overhaul.