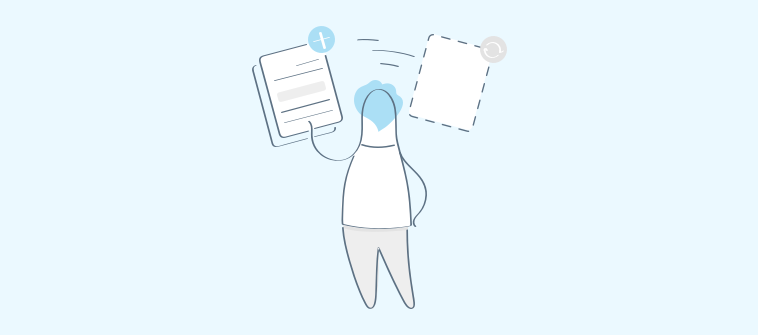
There are many aspects to risk management. It is important to identify threats and vulnerabilities, and develop a plan for responding. Once you have identified potential threats and vulnerabilities, you can start the process of assessing residual risks. The end result will give you a clear picture about what actions to take in order to reduce the impact. These are just some of the parts. Continue reading for more details. It is vital to create a risk management program in order for your business to be successful.
Assessing residual risks
A risk assessment is an evaluation of residual risks that could be associated with a product, service, or product. A residual risk is defined as a risk that is still present after all the controls have been implemented. The residual risk may be either intrinsic, mitigating or extrinsic. It is important that you determine how to deal with residual risk. Also, it is important to perform a preliminary treatment evaluation in order to identify areas of risk beyond your organization's tolerance. A residual risk assessment will indicate a percentage of treatment based upon the expected effectiveness.
The vendor's nature and the organization's risk appetite are key factors in determining whether residual risks should be acceptable. Small to medium-sized organizations don't typically have a risk appetite high enough to adopt a comprehensive risk management strategy, and so will use industry-standard or baseline risks as their guide. A residual risk calculation is also likely to be used by companies who measure their risks against industry standards. However, it is important to remember that these methods may lead to inaccurate reporting and a false impression of security.
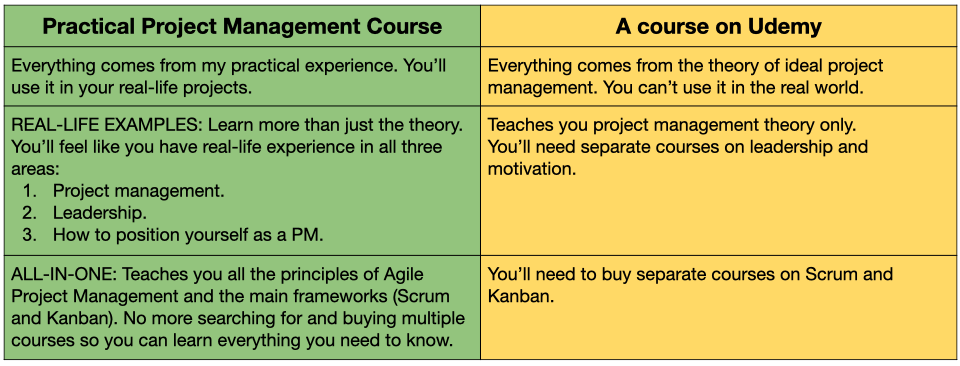
Identifying potential threats
As part of the risk management process, an organization should identify the different threats it may be exposed to. The first step in risk management involves identifying the threats that may affect the business. Many risk factors are known by businesses. Nevertheless, it's vital for employers to consider the threat landscape at every location. Identifying threats can be accomplished by reading industry publications, participating in industry conferences, and obtaining case studies. Some resources even provide metrics specific to the industry.
It is crucial to understand the potential threats and their likelihood. A threat can be categorized into three types: medium, high, or low impact. Threats can cause damage to your reputation, business operations, assets and reputation. These categories help you determine the risk to your business. You can also estimate the cost to mitigate a specific risk.
Identifying vulnerabilities
It is crucial to your business's security that you identify and manage vulnerabilities. This starts by defining your system baseline and determining your risk tolerance. Next, identify assets, weaknesses, risks, and threats. Then, you prioritize the fixes. Also, it is important to document all vulnerabilities. Non-technical management must be able to read and understand this documentation. Here are some tips and tricks to help make the vulnerability management process go as smoothly as possible.
It is essential to identify your vulnerabilities. This will help you prioritize security efforts and decrease risk faster. There are many tools that will help you identify your vulnerabilities and provide the best solutions. Some systems assist you in identifying the most dangerous vulnerabilities first. This will reduce the likelihood of a breach by removing the highest-risk vulnerabilities first. By evaluating the vulnerabilities, you can prioritize your security efforts based on the severity of threats.
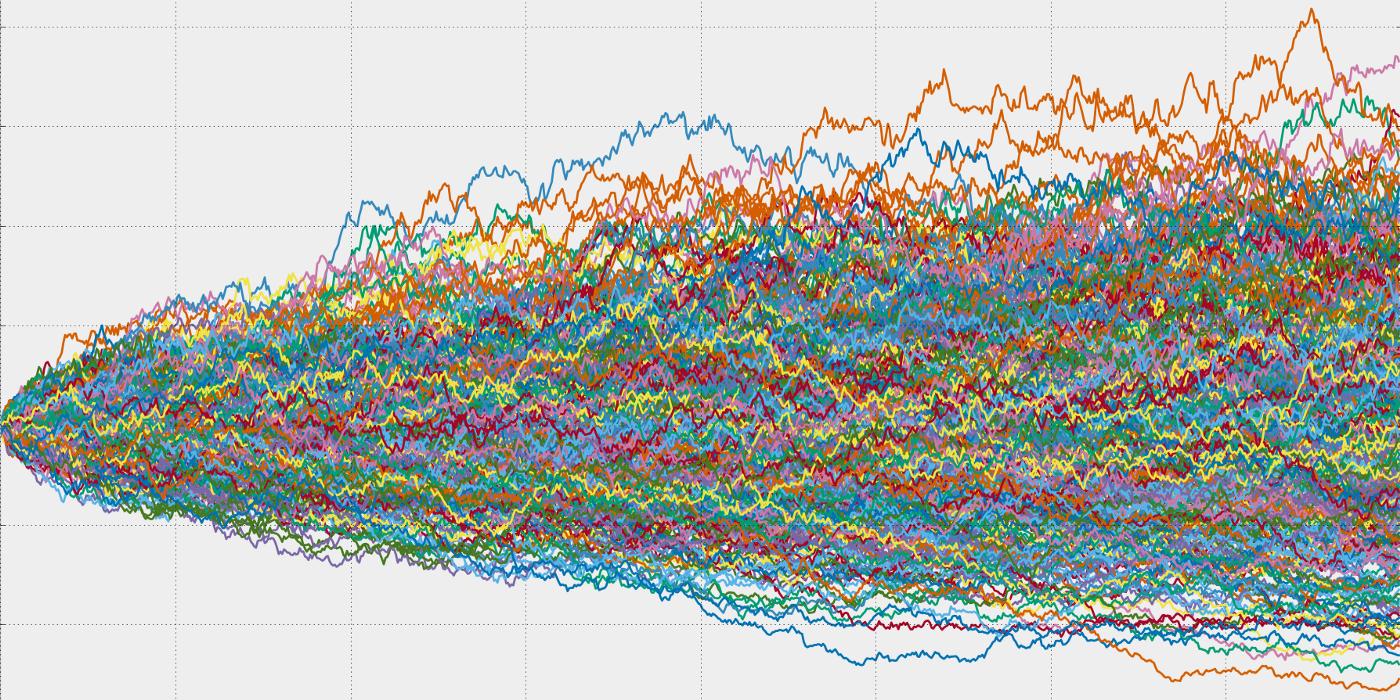
Develop a plan for responding
Developing a response plan as part of the risk management process is vitally important. Each risk category has its own requirements. These responses must be realistic and cost-effective within the context for the project. There are many options available for creating a plan to respond to a potential risk. This article will examine some of the more common ways to plan response plans for each category.
Each risk comes with a variety of strategies. The best risk management strategy is the one that reduces or eliminates all associated risks. You can use risk analysis tools to identify these strategies. The next step is to plan specific actions to implement these strategies. Fallback plans should be included in case the strategies don’t work. You should allocate contingency funds based on the project’s risk thresholds, and a quantitative analysis of the risk.
FAQ
Why is it so hard to make smart business decisions?
Complex systems with many moving parts are the hallmark of businesses. They require people to manage multiple priorities and deal with uncertainty and complexity.
It is important to understand the effects of these factors on the system in order to make informed decisions.
This requires you to think about the purpose and function of each component. You then need to consider how those individual pieces interact with each other.
Also, you should ask yourself if there have been any assumptions in your past behavior. You might consider revisiting them if they are not.
If you're still stuck after all this, try asking someone else for help. They might have different perspectives than you, and could offer insight that could help you solve your problem.
What role does a manager have in a company's success?
Managers' roles vary from industry to industry.
A manager is generally responsible for overseeing the day to day operations of a company.
He/she ensures the company meets its financial commitments and produces goods/services that customers demand.
He/she is responsible for ensuring that employees comply with all regulations and follow quality standards.
He/she plans and oversees marketing campaigns.
What are the three main management styles you can use?
There are three main management styles: participative, laissez-faire and authoritarian. Each style has its own strengths and weaknesses. Which style do yo prefer? Why?
Autoritarian – The leader sets the direction for everyone and expects them to follow. This style works well if an organization is large and stable.
Laissez-faire is a leader who allows everyone to make their own decisions. This style works best when an organization is small and dynamic.
Participative: The leader listens to everyone's ideas and suggestions. This style works best in smaller organizations where everyone feels valued.
What is the difference in leadership and management?
Leadership is about being a leader. Management is about controlling others.
A leader inspires his followers while a manager directs the workers.
A leader motivates people and keeps them on task.
A leader develops people; a manager manages people.
Why is project management so important?
To ensure projects run smoothly and meet deadlines, project management techniques are employed.
Because most businesses depend heavily on project work to produce goods or services,
These projects require companies to be efficient and effective managers.
Companies can lose time, money, and reputation if they don't have a good project management system.
Statistics
- The profession is expected to grow 7% by 2028, a bit faster than the national average. (wgu.edu)
- Our program is 100% engineered for your success. (online.uc.edu)
- The BLS says that financial services jobs like banking are expected to grow 4% by 2030, about as fast as the national average. (wgu.edu)
- 100% of the courses are offered online, and no campus visits are required — a big time-saver for you. (online.uc.edu)
- As of 2020, personal bankers or tellers make an average of $32,620 per year, according to the BLS. (wgu.edu)
External Links
How To
How is Lean Manufacturing done?
Lean Manufacturing methods are used to reduce waste through structured processes. They were created in Japan by Toyota Motor Corporation during the 1980s. The main goal was to produce products at lower costs while maintaining quality. Lean manufacturing eliminates unnecessary steps and activities from a production process. It consists of five basic elements: pull systems, continuous improvement, just-in-time, kaizen (continuous change), and 5S. Pull systems are able to produce exactly what the customer requires without extra work. Continuous improvement refers to continuously improving existing processes. Just-in–time refers when components or materials are delivered immediately to their intended destination. Kaizen means continuous improvement, which is achieved by implementing small changes continuously. Five-S stands for sort. It is also the acronym for shine, standardize (standardize), and sustain. These five elements are used together to ensure the best possible results.
Lean Production System
Six key concepts are the basis of lean production:
-
Flow - focuses on moving information and materials as close to customers as possible.
-
Value stream mapping- This allows you to break down each step of a process and create a flowchart detailing the entire process.
-
Five S's: Sort, Shine Standardize, Sustain, Set In Order, Shine and Shine
-
Kanban – visual signals like colored tape, stickers or other visual cues are used to keep track inventory.
-
Theory of constraints: identify bottlenecks in your process and eliminate them using lean tools, such as kanban board.
-
Just-intime - Order components and materials at your location right on the spot.
-
Continuous improvement: Make incremental improvements to the process instead of overhauling it completely.