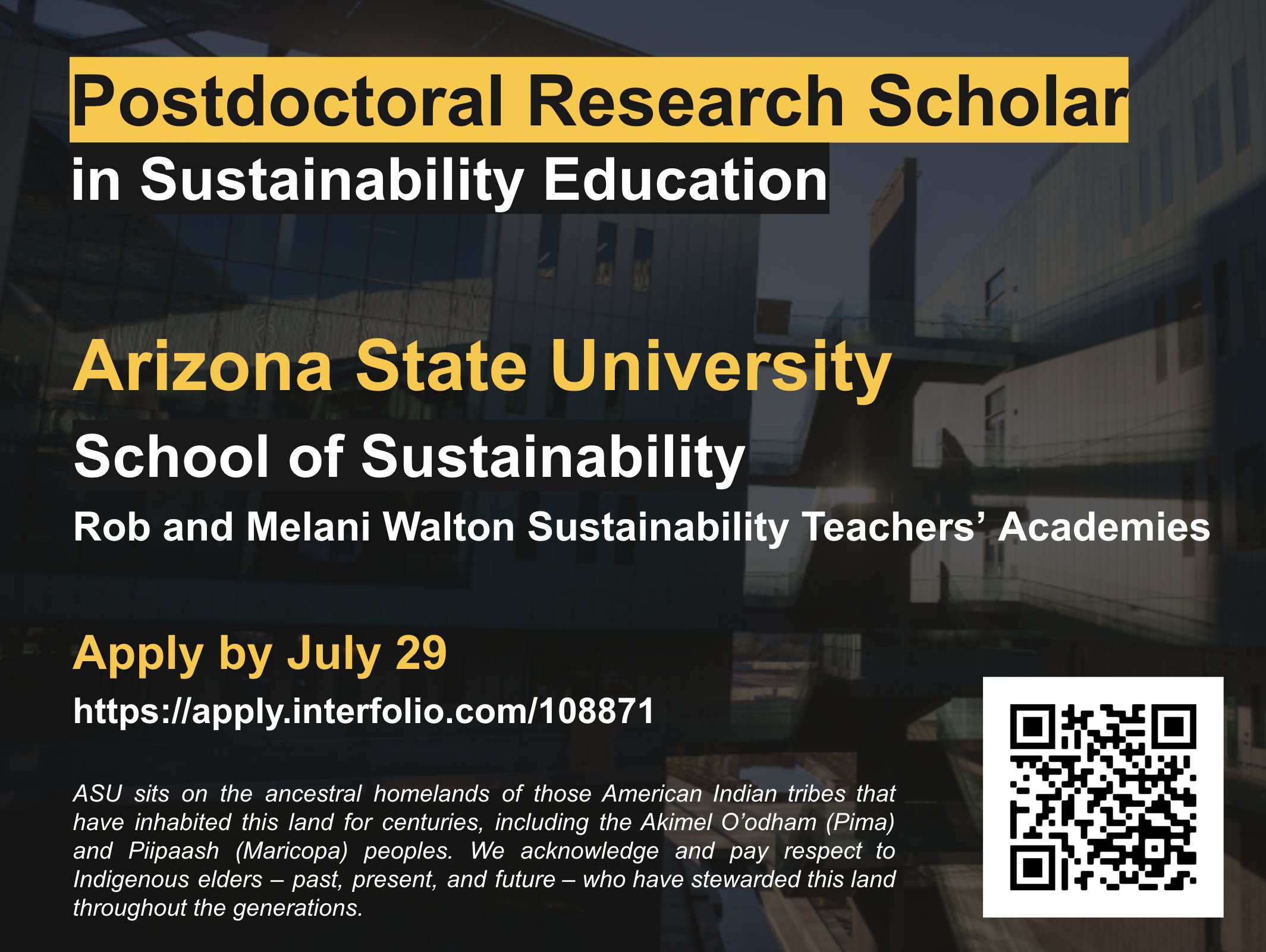
If you are looking for practical and strategic approach to managing global supply chains, this book will prove to be a useful guide for you. This book presents a systematic, comprehensive and easy to understand content that will be helpful for practitioners and researchers. This book is highly recommended. It covers the essential concepts and processes of strategic Supply Chain Management. The authors offer a step-bystep approach to achieve strategic supply chain objectives. Practitioners and researchers alike will enjoy this book.
Demand-driven supply chain
A demand-driven supply chain is a strategic supply chain in which the entire chain responds to changes in demand. Companies are able anticipate and fulfill customer orders in real time. This is different from the traditional model where the supplier announces availability and the retailer takes delivery. This model helps companies improve their efficiency and maintain control over inventories. Companies can meet customer demands quicker and more efficiently by using demand-driven supply channels.
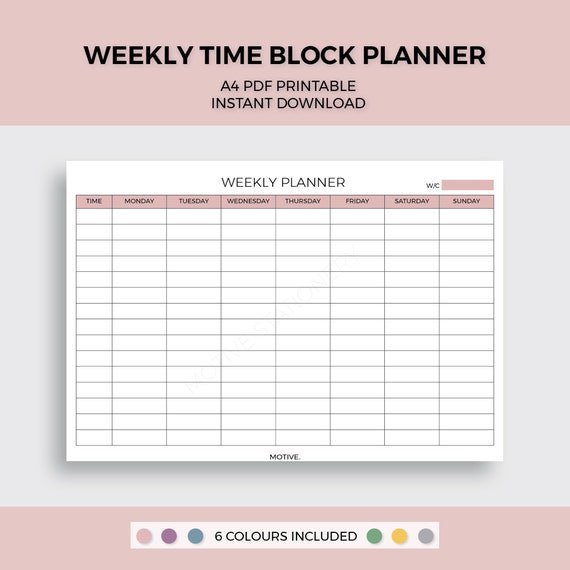
Planning
The supply chain planning and optimization tools used by organizations are organizational-based. There are many planning methods that support different levels of decision-making. A successful company should conduct annual strategic business plans and identify potential opportunities for growth. Many organizations use software that helps them optimize and plan their supply chain. Below is a discussion of the various planning methods. You can choose the one that suits your preference.
Execution
The formal management of a company's supply chain network is called strategic supply chain management. A supply chain manager creates a strategy that maximizes value, efficiency, resilience. The strategy should align with the company’s business strategy. It takes careful planning and execution to manage your supply chain. The key is to understand your supply chain and its role in your business strategy. Here are some ways to manage your supply chain effectively. Establish a vision for your supply chains.
Monitoring
Effective management depends on information. Ineffective management is possible when managers lack the data and tools needed to make informed decisions. Managers who aren't diligent in monitoring supply chains are less prepared to deal with disruptions and other potential hazards as they grow in complexity. Supply chain monitoring has become a must. Monitoring your supply chains has many benefits. Here are just few. You can read on to learn more.
Sustainability
It's difficult to ensure true sustainability in a supply chain. It is more challenging to achieve true sustainability in a strategic supply chain that is more complicated. Therefore, the procurement team should designate a sustainability point person to lead the sustainability process and regularly assess the progress of main suppliers. The procurement department should also define sustainability goals that the team will require suppliers to reach. The whole process will become transparent. It is a good way to gauge supplier performance by measuring the number of services or products that support the company's sustainability goals.
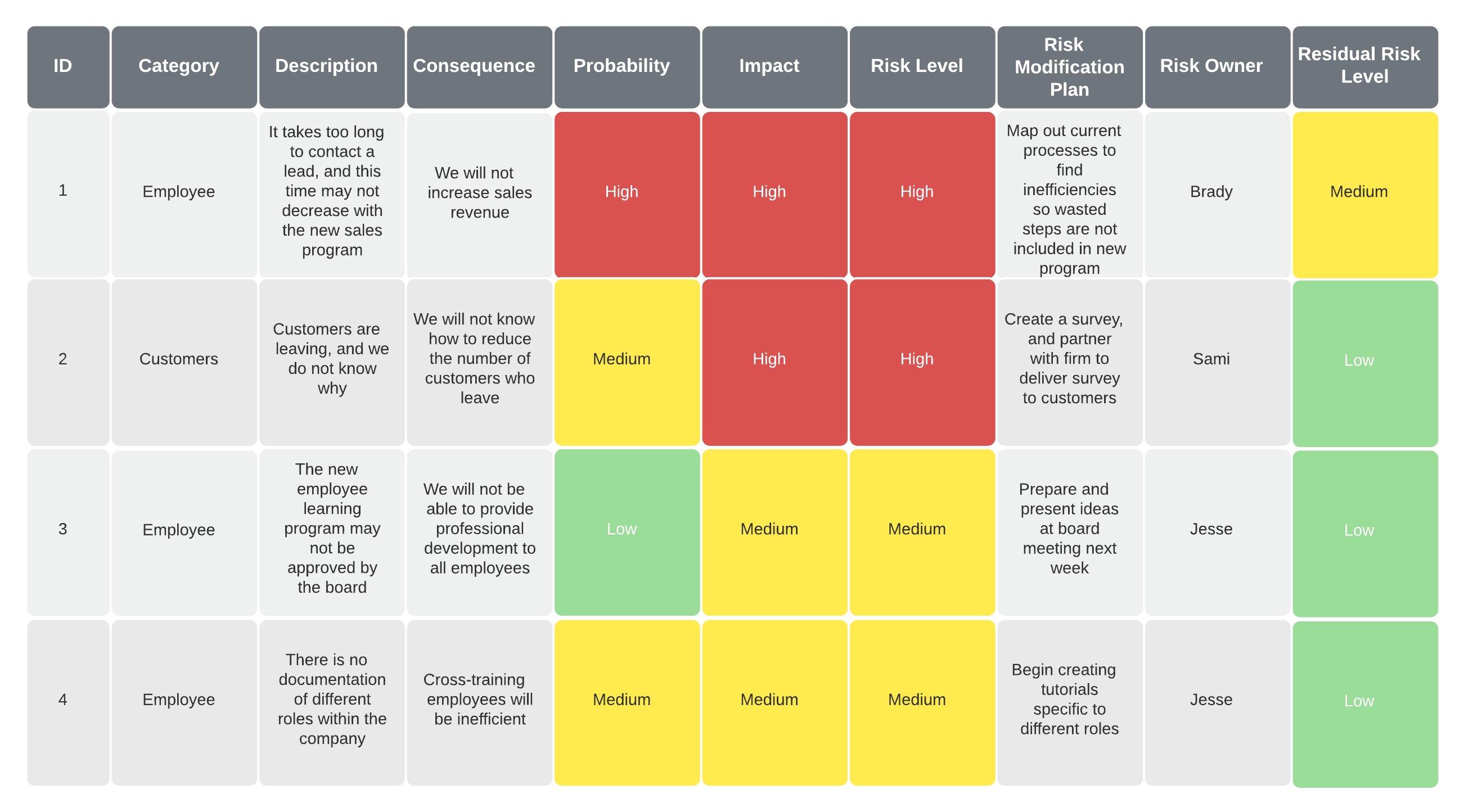
Variations depending on the product type
Companies should offer a broad range of products to consumers in order to maximize their performance. But they launch new product variants without considering whether they will create additional complexity within their supply chain. Consumer-goods companies saw a 60 percent increase in the number of new products that they introduced each year from 2002 to 2011. This increased demand caused an increase of costs in their supply chains. For example, in the same period, U.S. consumer-goods companies increased the number of new products they introduced annually by 60 percent. This resulted in higher costs for many areas of the supply chain but only 2.8% per annum.
FAQ
Why does it sometimes seem so difficult to make good business decisions?
Complex systems are often complex and have many moving parts. People who manage them have to balance multiple priorities while dealing with complexity and uncertainty.
To make good decisions, you must understand how these factors affect the entire system.
It is important to consider the functions and reasons for each part of the system. You then need to consider how those individual pieces interact with each other.
It is also worth asking yourself if you have any unspoken assumptions about how you have been doing things. If so, it might be worth reexamining them.
For help, ask someone else if you're still stumped after all the above. They might see things differently than you and may have some insights that could help find a solution.
What is the difference between Six Sigma Six Sigma and TQM?
The major difference between the two tools for quality management is that six Sigma focuses on eliminating defect while total quality control (TQM), on improving processes and decreasing costs.
Six Sigma can be described as a strategy for continuous improvement. This approach emphasizes eliminating defects through statistical methods like control charts, Pareto analysis, and p-charts.
This method aims to reduce variation in product production. This is accomplished by identifying the root cause of problems and fixing them.
Total quality management is the measurement and monitoring of all aspects within an organization. It also includes the training of employees to improve performance.
It is frequently used as an approach to increasing productivity.
How can a manager enhance his/her leadership skills?
By practicing good management skills at all times.
Managers must constantly monitor the performance of their subordinates.
You must act quickly if you notice that your subordinate isn’t performing to their standards.
It is essential to know what areas need to be improved and how to do it.
Statistics
- The profession is expected to grow 7% by 2028, a bit faster than the national average. (wgu.edu)
- UpCounsel accepts only the top 5 percent of lawyers on its site. (upcounsel.com)
- 100% of the courses are offered online, and no campus visits are required — a big time-saver for you. (online.uc.edu)
- Your choice in Step 5 may very likely be the same or similar to the alternative you placed at the top of your list at the end of Step 4. (umassd.edu)
- This field is expected to grow about 7% by 2028, a bit faster than the national average for job growth. (wgu.edu)
External Links
How To
How can you implement a Quality Management Plan?
The Quality Management Plan (QMP) was established in ISO 9001. It is a systematic way to improve processes, products and services. It focuses on the ability to measure, analyze and control processes and customer satisfaction.
QMP stands for Quality Management Process. It is used to guarantee good business performance. QMP's goal is to improve service delivery and production. A QMP should include all three aspects - Processes, Products, and Services. If the QMP focuses on one aspect, it is called "Process." QMP. If the QMP is focused on a product/service, it's called a QMP. And when the QMP concentrates on Customer Relationships, it is called "Customer" QMP.
There are two key elements to implementing a QMP: Strategy and Scope. They are defined as follows:
Scope: This defines what the QMP will cover and its duration. This will be used to define activities that are performed in the first six months of a QMP.
Strategy: These are the steps taken in order to reach the goals listed in the scope.
A typical QMP has five phases: Planning (Design, Development), Implementation (Implementation), and Maintenance. Each phase is explained below:
Planning: This stage identifies and prioritizes the QMP's objectives. Every stakeholder involved in the project is consulted to determine their expectations and needs. The next step is to create the strategy for achieving those objectives.
Design: In this stage, the design team designs the vision and mission, strategies, as well as the tactics that will be required to successfully implement the QMP. These strategies are executed by creating detailed plans.
Development: Here, the team develops the resources and capabilities that will support the successful implementation.
Implementation: This is the actual implementation and use of the QMP's planned strategies.
Maintenance: This is an ongoing process to maintain the QMP over time.
In addition, several additional items must be included in the QMP:
Stakeholder Engagement: It is crucial for the QMP to be a success. They should actively be involved during the planning and development, implementation, maintenance, and design stages of QMP.
Initiation of a Project: A clear understanding and application of the problem statement is crucial for initiating a project. In other words, the initiator needs to know why they want to do something and what they expect from the outcome.
Time Frame: This is a critical aspect of the QMP. You can use a simplified version if you are only going to be using the QMP for short periods. For a long-term commitment you may need more complicated versions.
Cost Estimation. Cost estimation is another crucial component of QMP. You cannot plan without knowing how much money you will spend. Therefore, cost estimation is essential before starting the QMP.
QMPs are more than just documents. They can also be updated as needed. It evolves as the company grows and changes. It is important to review it periodically to ensure it meets all current requirements.