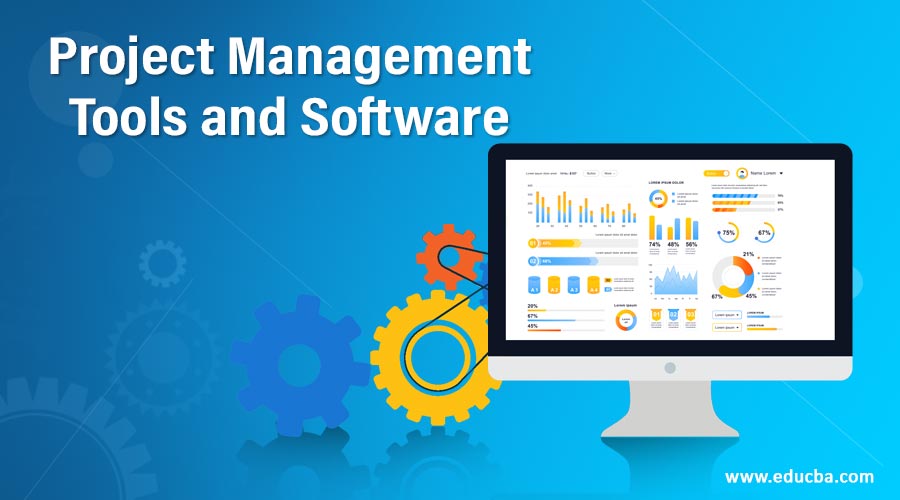
If you're considering renting a roll-off dumpster in Klamath Falls, you may be wondering how much the service will cost. When comparing dumpster rental companies, there are some things you need to keep in mind: Dumpster sizes, recycling and permit requirements. Once you have answered all these questions, you can choose a dumpster to start your project.
Klamath Falls dumpster rental cost
There are many factors that can affect the price of renting a dumpster Klamath Falls, OR. The first is how much space you need. For smaller homes, a small dumpster is not necessary. A 20-cubic yard dumpster is the best solution for large housecleanouts. This is a great option for large items, such as sheds or decks.
You should also consider the time period for which the dumpster will be needed. You can usually use the dumpster rental company's services for a specified number of days. The cost of renting a dumpster will increase the longer you keep it.
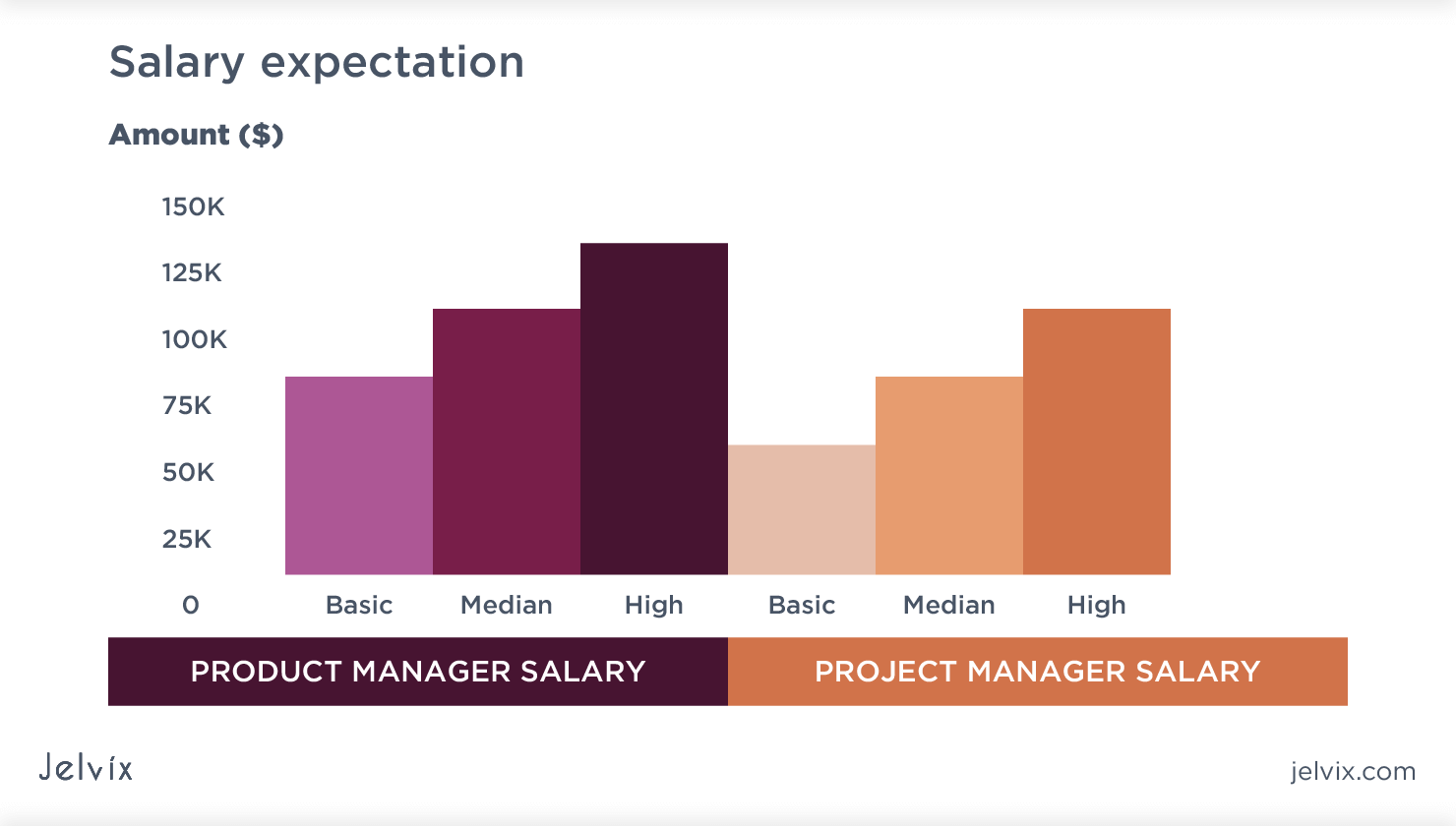
Dumpster sizes
You need to select the right size dumpster for your job if you are going to manage trash at your business or home. Proper dumpster size will ensure that you have enough room to dispose of your waste. Smaller dumpsters will cause loading and unloading to be more difficult and costlier. Dumpster rentals are important for a variety of projects, including home renovations, remodeling, and even junk removal.
Asking for quotes from different companies around your area is the best way find a low-cost dumpster rental. You will be able compare prices and select the company that offers the best size dumpster for your project. It is important to remember that not all companies will charge extra for specific services such as pick up and drop off. You will get the best price if you request a quote that includes all services. Certain materials may be thrown away at a higher rate by some companies.
Recycling efforts
The Valley Community for Recycling Solutions is making a big push to increase recycling awareness and increase the volume of recyclable materials. This includes the construction of a new drop off facility. Valley Community for Recycling Solutions intends to raise recycling awareness by expanding education and outreach programs. It is also attempting to raise $1,000,000 in grant money.
The company also plans to expand its recycling services at Klamath Falls. This will be done in partnership with Waste Management and Klamath County Solid Waste. Reach purchased a recycling line from Roseburg to help with the expansion. It cost approximately $5000.
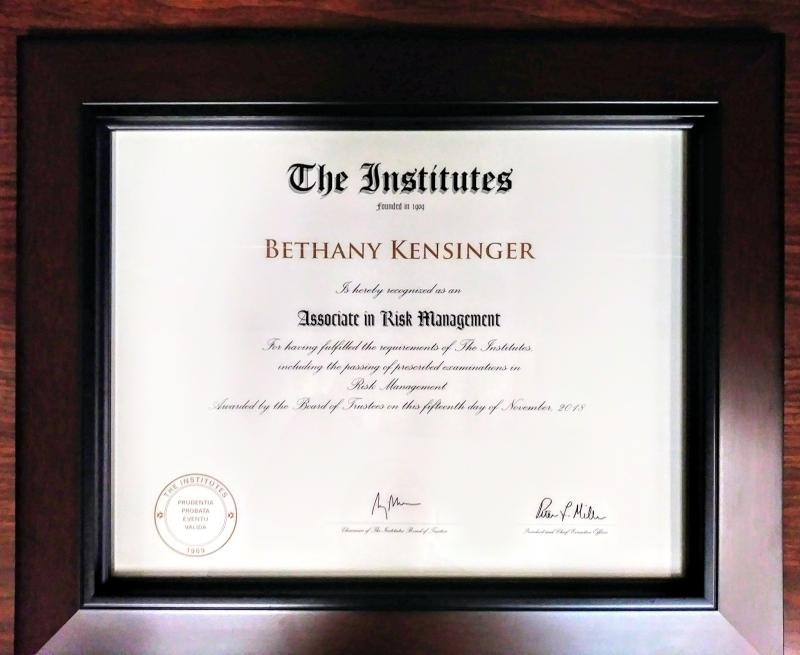
Permit requirements
The City of Klamath Falls has a Solid Waste Division that collects and disposes of solid waste. The division also offers recycling, reuse and litter prevention services. Customers who live in residential areas may bring up to three bags for yard waste and a 32-gallon trash can on their service days.
Klamath Falls' waste management regulations vary depending on the kind of waste being disposed of. You may be required to obtain a permit if you're going to dispose of hazardous or putrescible waste. Hazardous wastes, like lead acid batteries, need to be properly transported and disposed. In addition, if you're disposing of hazardous materials, you'll need to follow the Department of Environmental Quality's requirements for hazard-free waste disposal.
FAQ
How can we make our company culture successful?
A company culture that values and respects its employees is a successful one.
It is based on three principles:
-
Everybody has something of value to share
-
People are treated fairly
-
There is mutual respect between individuals and groups
These values are reflected by the way people behave. For example, they will treat others with courtesy and consideration.
They will be respectful of the opinions of other people.
These people will inspire others to share thoughts and feelings.
Company culture also encourages open communication, collaboration, and cooperation.
People feel safe to voice their opinions without fear of reprisal.
They know mistakes will be accepted as long as they are dealt with honestly.
Finally, the company culture encourages honesty as well as integrity.
Everyone is aware that truth must be told.
Everyone understands there are rules that they must follow.
No one is entitled to any special treatment or favors.
How can a manager enhance his/her leadership skills?
Good management skills are essential for success.
Managers must monitor the performance of subordinates constantly.
It is important to take immediate action if your subordinate doesn't perform as expected.
It is essential to know what areas need to be improved and how to do it.
How do you manage your employees effectively?
The key to effective management of employees is ensuring their happiness and productivity.
This also involves setting clear expectations and monitoring their performance.
Managers need clear goals to be able to accomplish this.
They should communicate clearly with employees. They should also ensure that they both reward high performers and discipline those who are not performing to their standards.
They will also need to keep records about their team's activities. These include:
-
What was accomplished?
-
How much work was done?
-
Who did it and why?
-
How did it get done?
-
Why did it happen?
This data can be used to evaluate and monitor performance.
What kind of people use Six Sigma?
People who have worked with statistics and operations research will usually be familiar with the concepts behind six sigma. Anyone involved in business can benefit.
It requires high levels of commitment and leadership skills to be successful.
What role can a manager fill in a company’s management?
Managers' roles vary from industry to industry.
A manager is generally responsible for overseeing the day to day operations of a company.
He/she ensures the company meets its financial commitments and produces goods/services that customers demand.
He/she will ensure that employees follow all rules and regulations, and adhere to quality standards.
He/she plans new products and services and oversees marketing campaigns.
What is a basic management tool used in decision-making?
A decision matrix can be a simple, but effective tool to assist managers in making decisions. It helps them to think strategically about all options.
A decision matrix is a way of representing alternatives as rows and columns. This makes it easy for you to see how each option affects other options.
In this example, there are four possible options represented by boxes on the left-hand side of the matrix. Each box represents an alternative. The status quo (the current condition) is shown in the top row, and what would happen if there was no change?
The effect of selecting Option 1 is shown in the middle column. In this example, it would lead to an increase in sales of between $2 million and $3 million.
The next two columns show the effects of choosing Options 2 and 3. These positive changes result in increased sales of $1 million and $500,000. They also have negative consequences. Option 2, for example, increases the cost by $100 000 while Option 3 decreases profits by $200 000.
The final column shows the results for Option 4. This means that sales will decrease by $1 million.
A decision matrix has the advantage that you don’t have to remember where numbers belong. Simply look at the cells to instantly determine if one choice is better than the other.
This is because the matrix has done all the hard work. It is as simple a matter of comparing all the numbers in each cell.
Here's a sample of how you might use decision matrixes in your business.
It is up to you to decide whether to spend more money on advertising. If you do, you'll be able to increase your revenue by $5 thousand per month. But, you will also incur additional expenses of $10 thousand per month.
By looking at the cell just below "Advertising", the net result can be calculated as $15 thousand. Therefore, you should choose to invest in advertising since it is worth more than the cost involved.
What are the main four functions of management
Management is responsible to plan, organize, direct, and control people and resources. It includes the development of policies and procedures as well as setting goals.
Organizations can achieve their goals through management. This includes leadership, coordination, control and motivation.
Management has four primary functions:
Planning - This is the process of deciding what should be done.
Organizing - Organization involves deciding what should be done.
Directing - This refers to getting people follow instructions.
Controlling – Controlling is the process of ensuring that tasks are completed according to plan.
Statistics
- This field is expected to grow about 7% by 2028, a bit faster than the national average for job growth. (wgu.edu)
- Our program is 100% engineered for your success. (online.uc.edu)
- Hire the top business lawyers and save up to 60% on legal fees (upcounsel.com)
- Your choice in Step 5 may very likely be the same or similar to the alternative you placed at the top of your list at the end of Step 4. (umassd.edu)
- The profession is expected to grow 7% by 2028, a bit faster than the national average. (wgu.edu)
External Links
How To
What is Lean Manufacturing?
Lean Manufacturing methods are used to reduce waste through structured processes. These processes were created by Toyota Motor Corporation, Japan in the 1980s. The aim was to produce better quality products at lower costs. Lean manufacturing is about eliminating redundant steps and activities from the manufacturing process. It is composed of five fundamental elements: continuous improvement; pull systems, continuous improvements, just-in–time, kaizen, continuous change, and 5S. Pull systems are able to produce exactly what the customer requires without extra work. Continuous improvement is the continuous improvement of existing processes. Just-in–time refers when components or materials are delivered immediately to their intended destination. Kaizen means continuous improvement, which is achieved by implementing small changes continuously. The 5S acronym stands for sort in order, shine standardize and maintain. These five elements are combined to give you the best possible results.
Lean Production System
Six key concepts underlie the lean production system.
-
Flow - The focus is on moving information and material as close as possible to customers.
-
Value stream mapping- This allows you to break down each step of a process and create a flowchart detailing the entire process.
-
Five S's - Sort, Set In Order, Shine, Standardize, and Sustain;
-
Kanban – visual signals like colored tape, stickers or other visual cues are used to keep track inventory.
-
Theory of constraints - identify bottlenecks in the process and eliminate them using lean tools like kanban boards;
-
Just-intime - Order components and materials at your location right on the spot.
-
Continuous improvement - make incremental improvements to the process rather than overhauling it all at once.