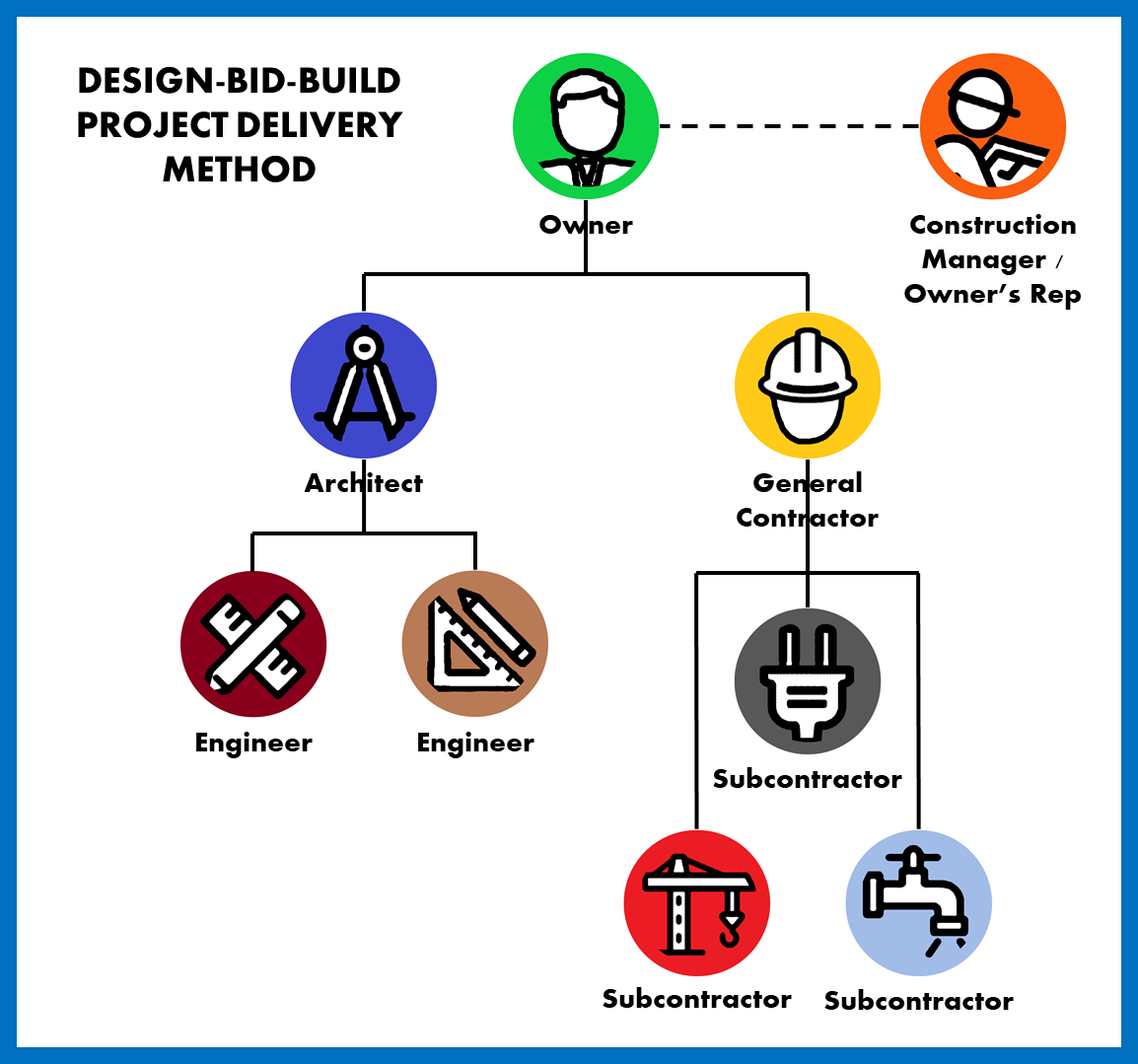
Cyber-risk is any type or risk that involves the use information technology. Information technology risks can range from data breaches to access risk. These risks are related to both business and personal data, and need to be properly managed. This article will provide you with information on the various risks associated with IT. It will also help to determine the best controls for your business.
Information technology risk
Information technology risk, also known as cyber risk, is any risk associated with information technology. This type of threat is most common among startups and small businesses. But larger businesses must consider information security risks in order to protect their business continuity. Cyber attacks can be mitigated and businesses protected from any negative consequences.
It is essential to have a holistic and systematic approach when managing information technology risks. This requires systematic risk analysis as well as systemic risk management. It requires decision-makers who have the ability to reverse previous decisions and a clear communication structure.
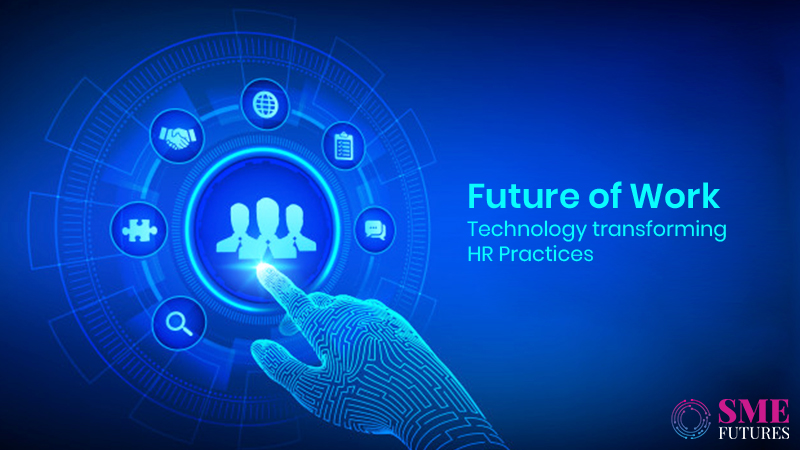
Data breach risk
Data breaches are when unauthorised individuals access, steal, modify, or alter data on a computer system. This can cause financial loss, reputational damage and lawsuits. It can also affect the security of government agencies' systems. High-sensitive information can also be exposed by breaches. An attacker could also gain access to trade secrets if they are able to hack into the IT infrastructure of the government. A third party can use the data to create fraudulent accounts or sell it on darknet.
Once an IT risk like a data breach happens, a company should notify its customers and employees and implement a response plan to minimize the negative impact. This plan should be an ongoing document and updated as needed.
Access risk
Access risk is a concern in IT security. It refers to the risk of unauthorized access to vital information. Access can be from both logical and physical access. Physical access is the ability to access sensitive information like databases and processing environments. The network is used to connect users to these systems. The network may allow an employee to gain unauthorised access confidential or proprietary information.
It can be difficult to manage access permissions. There are many permission models for different applications and systems, which makes it hard to assign the correct permissions to each individual user. Organizations should have policies that restrict access to certain users in order to reduce this risk.
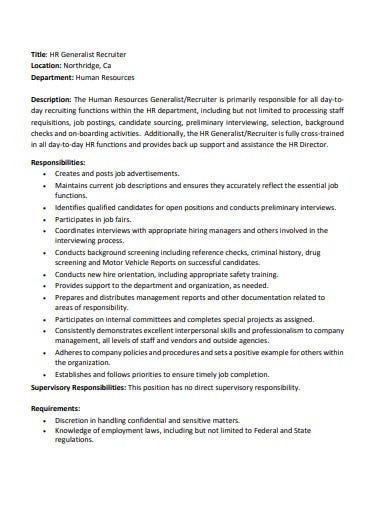
Control measures
You can take a variety of measures to reduce IT risk. You can reduce exposure to IT hazards by implementing physical security measures, training staff, or providing equipment. Control measures should be comprehensive and work together to reduce risk. You must also use administrative controls such job rotations to limit exposure. It is essential to have PPE, such as respirators and goggles. All of these measures must work together and be communicated and reviewed regularly to employees.
The basis of risk control measures should be based upon a risk assessment. In other words, you need to identify the risks that are most significant to your business and determine the best controls. These measures should be cost effective and efficient.
Reaction preparation
Workers should be aware of the risks associated with a specific reaction and pay particular attention to safety aspects during reaction preparation. Workers in the C and D categories should not be exposed to undue risk. However, workers in A need to be mindful of potential dangers related to carcinogens. Also, workers need to be aware about explosion risks.
FAQ
What is the meaning of "project management?"
We mean managing the activities involved in carrying out a project.
These include planning the scope and identifying the needs, creating the budget, organizing the team, scheduling the work and monitoring progress. Finally, we close down the project.
How can a manager enhance his/her leadership skills?
Through demonstrating good management skills at every opportunity
Managers must constantly monitor the performance of their subordinates.
You must act quickly if you notice that your subordinate isn’t performing to their standards.
You should be able pinpoint what needs to improve and how to fix it.
What are the three main management styles you can use?
These are the three most common management styles: participative (authoritarian), laissez-faire (leavez-faire), and authoritarian. Each style has its own strengths and weaknesses. Which style do your prefer? Why?
Authoritarian – The leader sets a direction and expects everyone follows it. This style works well if an organization is large and stable.
Laissez-faire: The leader lets each person decide for themselves. This style works best when the organization is small and dynamic.
Participative: The leader listens to everyone's ideas and suggestions. This is a great style for smaller organizations that value everyone.
Statistics
- The profession is expected to grow 7% by 2028, a bit faster than the national average. (wgu.edu)
- The average salary for financial advisors in 2021 is around $60,000 per year, with the top 10% of the profession making more than $111,000 per year. (wgu.edu)
- The BLS says that financial services jobs like banking are expected to grow 4% by 2030, about as fast as the national average. (wgu.edu)
- Our program is 100% engineered for your success. (online.uc.edu)
- Hire the top business lawyers and save up to 60% on legal fees (upcounsel.com)
External Links
How To
How is Lean Manufacturing done?
Lean Manufacturing is a method to reduce waste and increase efficiency using structured methods. They were created in Japan by Toyota Motor Corporation during the 1980s. It was designed to produce high-quality products at lower prices while maintaining their quality. Lean manufacturing emphasizes removing unnecessary steps from the production process. It includes five main elements: pull systems (continuous improvement), continuous improvement (just-in-time), kaizen (5S), and continuous change (continuous changes). Pull systems allow customers to get exactly what they want without having to do extra work. Continuous improvement is the continuous improvement of existing processes. Just-intime refers the time components and materials arrive at the exact place where they are needed. Kaizen is continuous improvement. This can be achieved by making small, incremental changes every day. Fifth, the 5S stand for sort, set up in order to shine, standardize, maintain, and standardize. To achieve the best results, these five elements must be used together.
The Lean Production System
Six key concepts form the foundation of the lean production system:
-
Flow - focuses on moving information and materials as close to customers as possible.
-
Value stream mapping - break down each stage of a process into discrete tasks and create a flowchart of the entire process;
-
Five S's - Sort, Set In Order, Shine, Standardize, and Sustain;
-
Kanban is a visual system that uses visual cues like stickers, colored tape or stickers to keep track and monitor inventory.
-
Theory of Constraints - Identify bottlenecks in the process, and eliminate them using lean tools such kanban boards.
-
Just-in-time delivery - Deliver components and materials right to your point of use.
-
Continuous improvement - make incremental improvements to the process rather than overhauling it all at once.