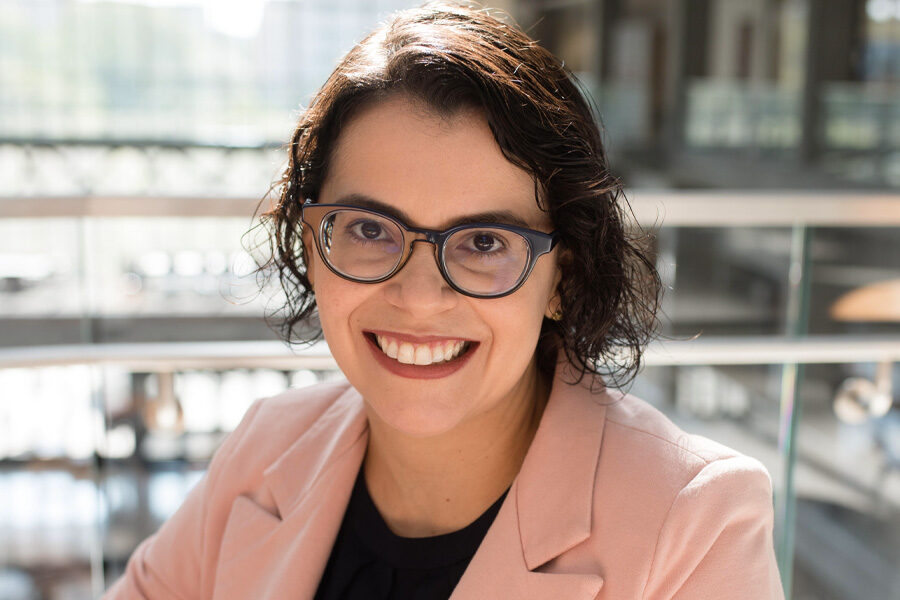
Clark Construction is one among the nation's most trusted general contractors. This means that interns can expect the best from top-notch construction professionals. Clark associate positions provide hands-on, real-world experience that prepares future construction professionals for their careers. You will be able to learn from the best construction professionals in the business and be a part of some of the most notable construction projects in the country.
Your job duties
Clark Construction internships are a great way to learn from top-notch construction professionals. As a Clark Construction intern, you will get to be part of some of the most important projects in the country and will also have the chance to gain firsthand knowledge about the business. These internships provide valuable hands-on experience and a realistic look at construction.
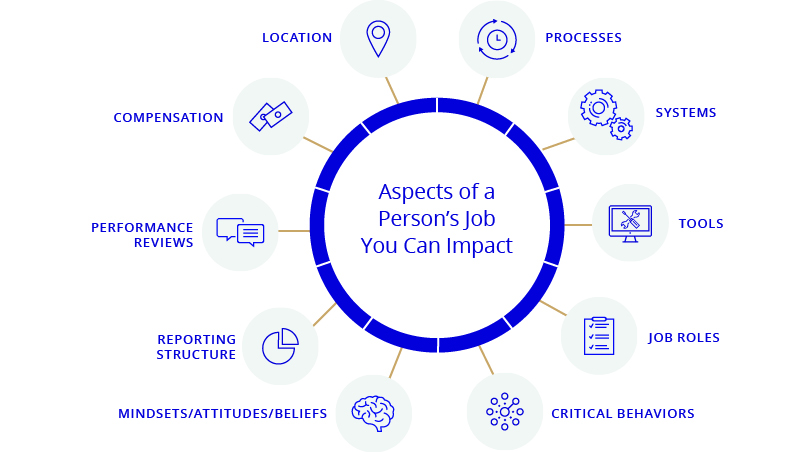
Along with your internship tasks on the jobsite you will also be able to work in many corporate offices. Learn about Clark's building process and how you can make a difference in the lives of others. Opportunities exist in Virtual Design & Construction, Research & Development, Scheduling, Safety, Sustainability, Talent Management, and Scheduling.
Salary
Clark Construction Group offers competitive salaries. Based on their compensation and perks, they rank among the top 15% of US companies. Clark Construction Group offers a great work environment and employees love their jobs. The company's turnover rate is low and employees are satisfied with their jobs, which is a significant advantage over its competition. In addition to high salaries, Clark Construction Group offers many other benefits, such as a paid internship.
Clark Construction Group's average salary is $106,341 per annum, or $51 per hour. It can vary by job, education level and department. The Director of Operations is the highest-paid position, with a salary of $331,673 per annum, while the Admin Assistant is the lowest paid, at $50,345 annually. The salary ranges for the Director of HR or Marketing are listed by department. They average $112,811 and $88,113, respectively.
Locate
Clark Construction may be a good choice if you are looking for a job as an intern. Clark Construction is consistently ranked among the top general contractors in the country. By working for Clark, you can learn from the top construction experts in the industry while building some of the most prestigious projects in the country. This internship allows you to get a more realistic look at construction and gives you valuable, hands-on experience.
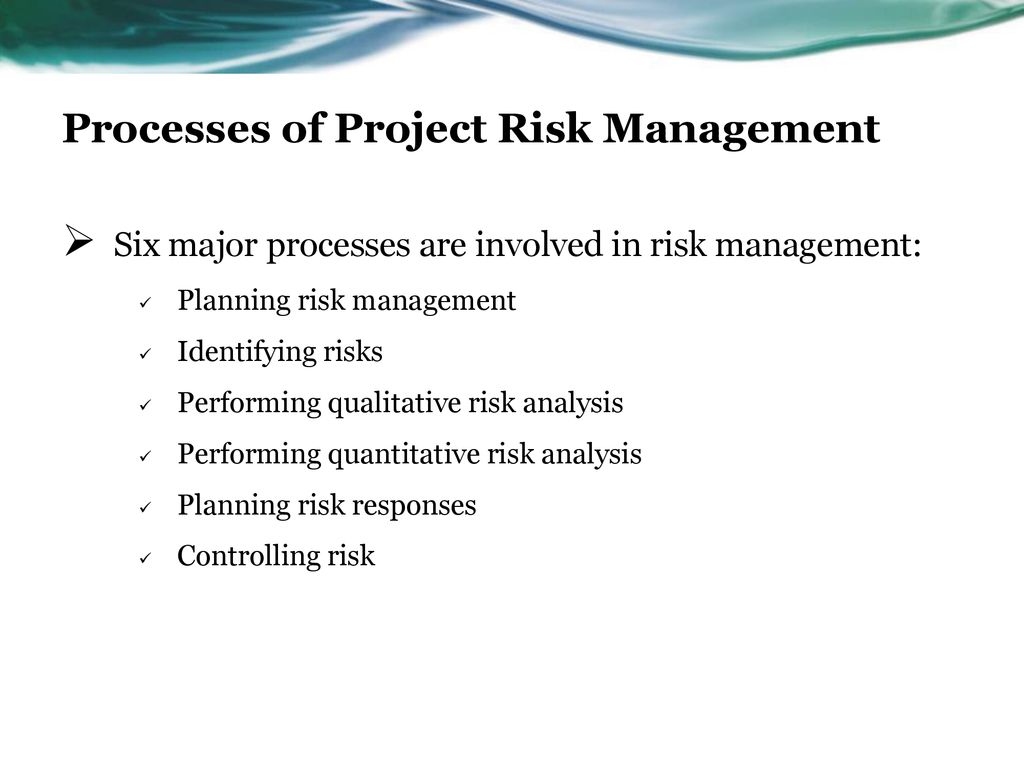
Clark Construction Group's employees are very happy at work. 86% report they love their jobs. In addition, only 20% of Clark Construction Group employees work less than eight hours a day. Clark, on the other hand, ranks third in overall culture. Clark employees are generally satisfied by their work, benefits, and company culture.
FAQ
What are the five management processes?
These five stages are: planning, execution monitoring, review and evaluation.
Setting goals for the future requires planning. Planning involves defining your goals and how to get there.
Execution is when you actually execute the plans. Everyone involved must follow them.
Monitoring is the process of evaluating your progress toward achieving your objectives. Regular reviews of performance against targets, budgets, and other goals should be part.
At the end of every year, reviews take place. They provide an opportunity to assess whether everything went well during the year. If not, it is possible to make improvements for next year.
After each year's review, evaluation occurs. It helps to identify what went well and what didn’t. It also provides feedback on the performance of people.
What does it mean to say "project management"
Management is the act of managing activities in order to complete a project.
Our services include the definition of the scope, identifying requirements, preparing a budget, organizing project teams, scheduling work, monitoring progress and evaluating the results before closing the project.
What is the difference between management and leadership?
Leadership is about influencing others. Management is all about controlling others.
A leader inspires others while a manager directs them.
A leader motivates people and keeps them on task.
A leader develops people; a manager manages people.
What is TQM?
When manufacturing companies realized that price was not enough to compete, the industrial revolution brought about the quality movement. To remain competitive, they had to improve quality as well as efficiency.
Management responded to the need to improve, and developed Total Quality Management (TQM). This focused on improving every aspect of an organization’s performance. It included continuous improvement processes, employee involvement, and customer satisfaction.
How can we make our company culture successful?
A company culture that values and respects its employees is a successful one.
It's built on three fundamental principles:
-
Everyone has something to contribute
-
Fair treatment of people is the goal
-
Respect is shared between individuals and groups
These values can be seen in the behavior of people. They will treat others with respect and kindness.
They will listen to other people's opinions respectfully.
And they will encourage others to share ideas and feelings.
The company culture promotes collaboration and open communication.
People are free to speak out without fear of reprisal.
They know that they will not be judged if they make mistakes, as long as the matter is dealt with honestly.
The company culture promotes honesty, integrity, and fairness.
Everyone understands that the truth is always best.
Everyone knows that there are rules and regulations that apply to them.
And no one expects special treatment or favors.
What are the four main functions of management?
Management is responsible of planning, organizing, leading, and controlling people as well as resources. This includes setting goals, developing policies and procedures, and creating procedures.
Management aids an organization in reaching its goals by providing direction and coordination, control, leadership motivation, supervision, training, evaluation, and leadership.
Management's four main functions are:
Planning – Planning involves deciding what needs to happen.
Organizing: Organizing refers to deciding how things should work.
Directing – This means to get people to follow directions.
Controlling – Controlling is the process of ensuring that tasks are completed according to plan.
Statistics
- As of 2020, personal bankers or tellers make an average of $32,620 per year, according to the BLS. (wgu.edu)
- Your choice in Step 5 may very likely be the same or similar to the alternative you placed at the top of your list at the end of Step 4. (umassd.edu)
- Hire the top business lawyers and save up to 60% on legal fees (upcounsel.com)
- 100% of the courses are offered online, and no campus visits are required — a big time-saver for you. (online.uc.edu)
- The average salary for financial advisors in 2021 is around $60,000 per year, with the top 10% of the profession making more than $111,000 per year. (wgu.edu)
External Links
How To
How does Lean Manufacturing work?
Lean Manufacturing processes are used to reduce waste and improve efficiency through structured methods. They were created by Toyota Motor Corporation in Japan in the 1980s. The main goal was to produce products at lower costs while maintaining quality. Lean manufacturing emphasizes removing unnecessary steps from the production process. It consists of five basic elements: pull systems, continuous improvement, just-in-time, kaizen (continuous change), and 5S. The production of only what the customer needs without extra work is called pull systems. Continuous improvement means continuously improving on existing processes. Just-in time refers to components and materials being delivered right at the place they are needed. Kaizen is continuous improvement. This can be achieved by making small, incremental changes every day. Last but not least, 5S is for sort. These five elements can be combined to achieve the best possible results.
Lean Production System
Six key concepts are the basis of lean production:
-
Flow - focus on moving material and information as close to customers as possible;
-
Value stream mapping- This allows you to break down each step of a process and create a flowchart detailing the entire process.
-
Five S's: Sort, Shine Standardize, Sustain, Set In Order, Shine and Shine
-
Kanban: Use visual signals such stickers, colored tape, or any other visual cues, to keep track your inventory.
-
Theory of Constraints - Identify bottlenecks in the process, and eliminate them using lean tools such kanban boards.
-
Just-in Time - Send components and material directly to the point-of-use;
-
Continuous improvement - make incremental improvements to the process rather than overhauling it all at once.