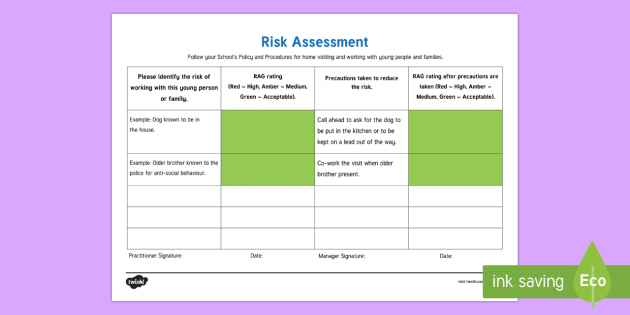
The supply chain is critical to creating strategic value for business owners and managers. It plays an important role in customer satisfaction and brand image as well as profitability. The supply chain can be transformed into a strategic asset by understanding its role in creating value. Here are some tips to maximize the supply chain's value.
E-commerce impacts on supply chain efficiency
The rapid growth of e-commerce has brought about many changes within the supply chain. With customers increasingly expecting faster deliveries, warehouses need to adapt to changing business practices to keep up with demand. 92% of UK households shop online, and the number of parcel deliveries is growing globally. These changes have affected the efficiency and effectiveness of the supply chain. They now have to cope with increasing production and delivery volumes. The transformation in the supply chain will continue for many more years.
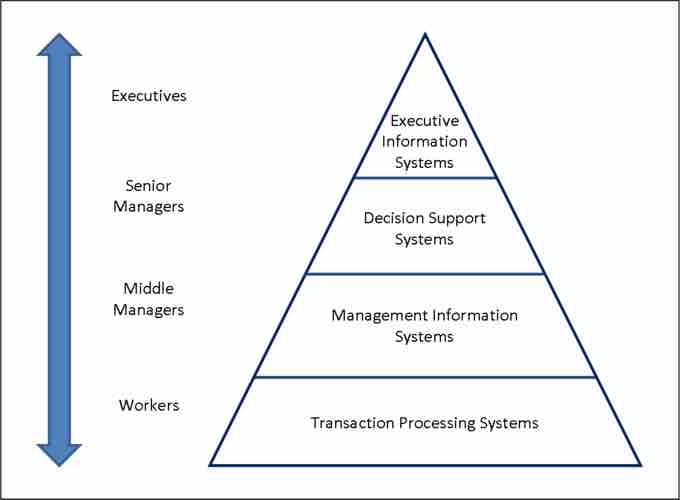
E-commerce is a way for companies and suppliers to communicate with each other. This eliminates the need to use paper or other manual processes. Additionally, companies can use e-commerce for transportation to cut down on costs. They can combine shipments with shipping carriers that offer discounts for bulk order. Further, e-commerce makes it possible for transportation businesses to share documents online during the fulfillment process, which can greatly improve the efficiency of the supply chain.
E-commerce has an impact on customer perceptions of value
E-commerce has revolutionized the way people shop and how companies work. Retailers struggled at first to meet the demands of consumers. Retailers struggled to keep up with the changing demands of the consumers as e-commerce developed. In the last decade, retailers focused on simplifying their processes to provide conveniences for customers. Technology such as curbside pickup and cybersecurity have made it easier for consumers to meet their needs.
E-commerce has also changed the way consumers buy and return products. Consumers can buy products instantly with a mobile device or via an e-store kiosk. They don't have to wait for delivery, or pay shipping. Consumers now expect free returns, and they will purchase more than they require. The new trends mean that the supply chains have to adapt to these new trends. In addition, e-commerce can impact the supply chain's productivity and inflation. The increased competition can reduce costs and push inflation downward.
Digitalization and the efficiency of supply chains
The use of digital technology can have a positive impact on supply chain efficiency. It improves the speed and cash flow of supply channels. Digital supply chain solutions, which connect disparate systems, allow for greater communication and efficiency throughout an organization. Companies will be able make faster decisions and decrease the chance of supply chain disruptions. These solutions also make the most of data that is available.
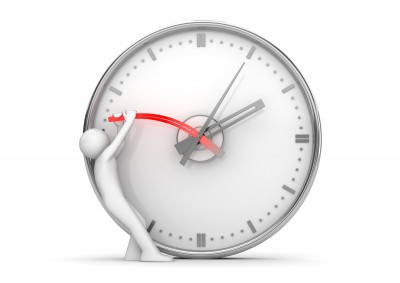
The supply chain will become increasingly digital as it requires more real-time information to make strategic decisions and optimize processes. Supply chain leaders with access to real data will be able better predict disruptions in supply chains and improve visibility throughout the chain. AI-powered analytical tools can also improve planning processes. This will allow companies to get actionable insights, which can help them avoid out of stock situations and adjust their inventories. The benefits of digitizing supply chains will also be seen in the ability to reduce lead times and lower costs.
FAQ
What is the difference between project and program?
A project is temporary; a program is permanent.
A project typically has a defined goal and deadline.
It is often carried out by a team of people who report back to someone else.
A program usually has a set of goals and objectives.
It is often implemented by one person.
What are management concepts, you ask?
Management Concepts are the management principles and practices that managers use in managing people and resources. They cover topics like job descriptions (job descriptions), performance evaluations, training programmes, employee motivation and compensation systems.
Why does it sometimes seem so difficult to make good business decisions?
Complex business systems have many moving parts. It is difficult for people in charge of businesses to manage multiple priorities simultaneously and also deal with uncertainty.
Understanding how these factors impact the whole system is key to making informed decisions.
You need to be clear about the roles and responsibilities of each system. Then, you need to think about how these pieces interact with one another.
You should also ask yourself if there are any hidden assumptions behind how you've been doing things. If they don't, you may want to reconsider them.
If you're still stuck after all this, try asking someone else for help. You may be able to see things from a different perspective than you are and gain insight that can help you find a solution.
What is TQM?
When manufacturing companies realized that price was not enough to compete, the industrial revolution brought about the quality movement. They needed to improve quality and efficiency if they were going to remain competitive.
To address this need for improvement management created Total Quality Management (TQM) which aimed to improve all aspects of an organization's performance. It included continuous improvement and employee involvement as well as customer satisfaction.
What are the 5 management processes?
These five stages are: planning, execution monitoring, review and evaluation.
Planning involves setting goals for the future. It involves setting goals and making plans.
Execution happens when you actually do the plan. Everyone involved must follow them.
Monitoring allows you to monitor your progress towards achieving your goals. Monitoring should include regular reviews of performance against goals and budgets.
At the end of every year, reviews take place. They give you an opportunity to review the year and assess how it went. If not, changes may be made to improve the performance next time around.
After each year's review, evaluation occurs. It helps to determine what worked and what didn’t. It also gives feedback on how well people did.
How does a manager learn to manage?
You can improve your management skills by practicing them at all times.
Managers must continuously monitor the performance levels of their subordinates.
It is important to take immediate action if your subordinate doesn't perform as expected.
You must be able to spot what is lacking and how you can improve it.
Statistics
- Hire the top business lawyers and save up to 60% on legal fees (upcounsel.com)
- This field is expected to grow about 7% by 2028, a bit faster than the national average for job growth. (wgu.edu)
- 100% of the courses are offered online, and no campus visits are required — a big time-saver for you. (online.uc.edu)
- UpCounsel accepts only the top 5 percent of lawyers on its site. (upcounsel.com)
- The average salary for financial advisors in 2021 is around $60,000 per year, with the top 10% of the profession making more than $111,000 per year. (wgu.edu)
External Links
How To
How do I get my Six Sigma license?
Six Sigma is a quality control tool that improves processes and increases efficiency. It is a method that enables companies to achieve consistent results with their operations. The name "Sigmas" comes from the Greek words "sigmas", meaning "six". Motorola was the first to develop this process. Motorola recognized that they had to standardize their manufacturing processes to produce faster and more affordable products. Due to the different workers involved, there was a lack of consistency. They used statistical tools such as Pareto analysis, control charts, and Pareto analysis to resolve the problem. Then they would apply the techniques to all parts of the operation. They would then be able make improvements where needed. When you are trying to obtain your Six Sigma certification, there are three steps. To determine whether you are qualified, the first step is to verify your eligibility. You will need classes to pass before you can begin taking tests. You can then start taking the tests once you have completed those classes. The class material will be reviewed. Next, you'll be ready for the test. If you pass, you'll get certified. And finally, you'll be able to add your certifications to your resume.