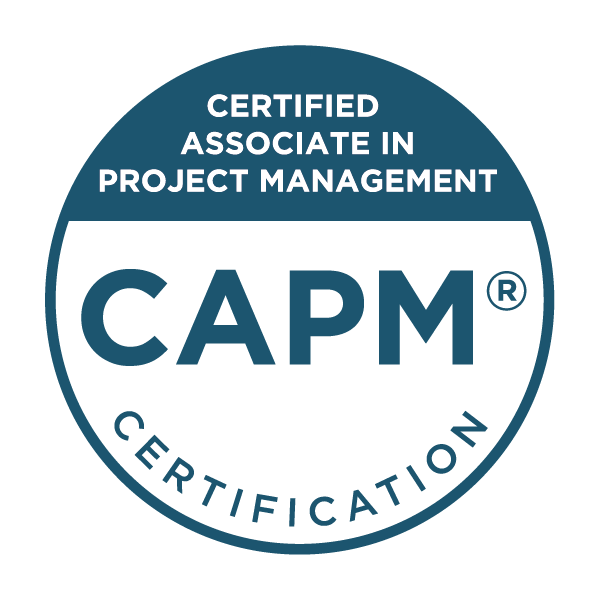
An ad hoc job is a job that can be used to describe a temporary job. This type is for people who have the skills required to work on the project and are willing to put in the time. Project managers will often consult other department managers to determine the amount of people needed to complete the job. The project managers will then have to make requests to the people qualified to complete it.
The management of ad hoc and emergency projects
A process for managing these projects is essential if your job involves you working on a variety of projects. You can achieve this by having a project diary that contains details about tasks, due dates, and other information. This will help you to remember the tasks, and it will also help you keep track of the work of others, which can improve communication and management. It is also important that the log be updated when new tasks are added, or changed.
Working on ad hoc tasks requires that everyone on the team understands what is expected. This is particularly important when the project involves collaboration between different stakeholders. You can't wait to see information trickle down through bureaucracy. Everyone in the team must be informed about the project's goals as well as its scope. If you are unsure of the project's goals, it is a good idea to ask for help from someone who does.
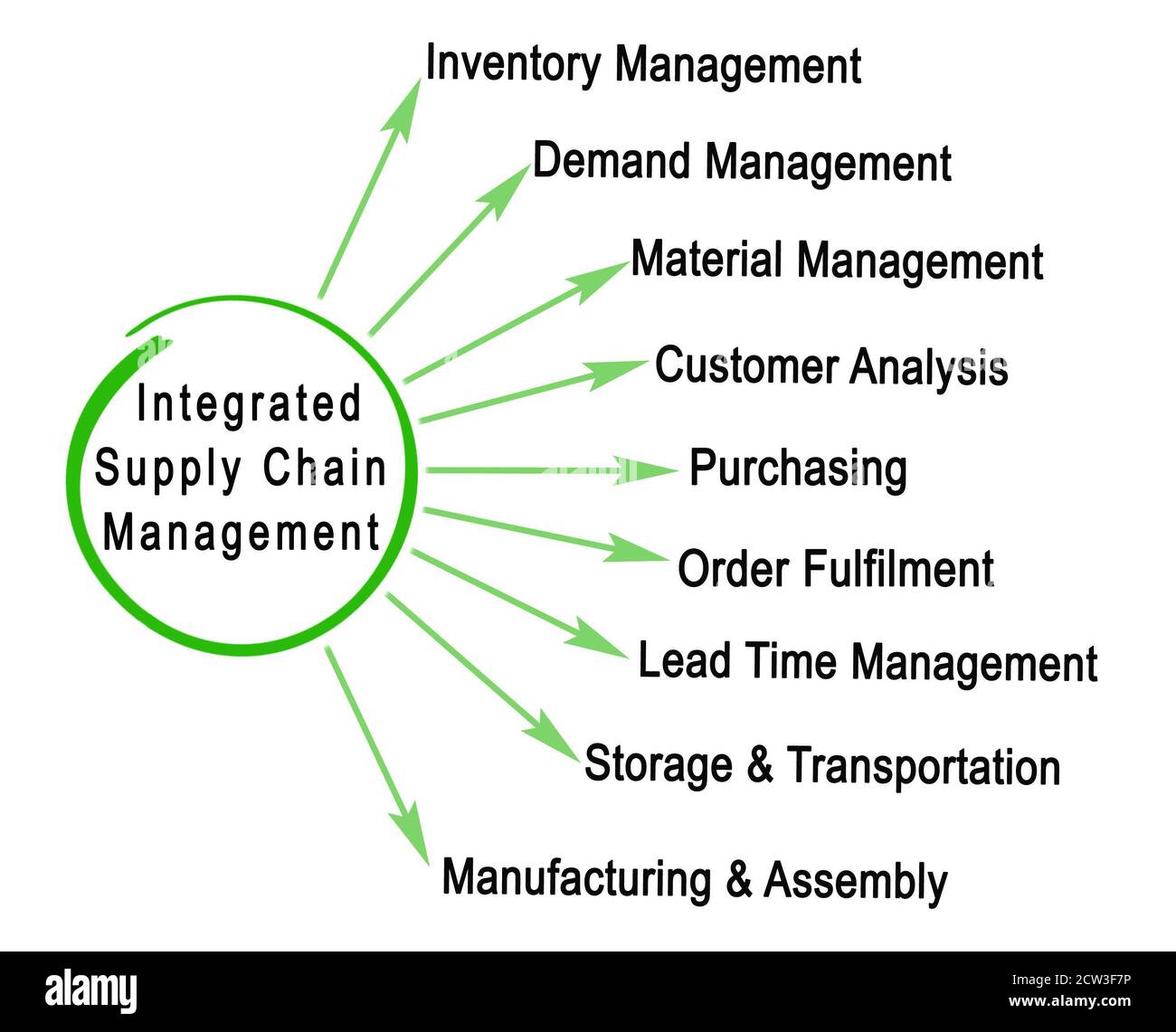
Ad hoc projects can be temporary and have no long-term commitments. These projects often have a short deadline and require multiple items. They also depend on multiple teams. Project managers will have to coordinate the team and assign resources.
Managing ad hoc employees
An ad-hoc job may require you to manage several people, some of whom may not be on your regular payroll. You will need to ensure that your employees have the right skills and the time necessary to complete the project. You may need to ask other managers from your department for assistance in such cases. Decide how many people you will need and send out requests for the necessary resources.
A good system can make managing ad-hoc projects easier. This will allow you to see the resources available and how they are being used. This will allow for better decision making regarding the project's management. It's crucial to keep track if you work with an ad hoc group.
You can either hire an outside contractor or internal employee to take on ad-hoc projects. They can be either full-time or part time and they are ideal for projects that don’t disrupt ongoing initiatives. However, if you're not prepared for the unexpected, you can end up with inefficiencies, waste resources, and miss your project goals.

Ad hoc requests are convenient but can cause chaos in your team. It is crucial that you prioritize requests from your marketing department and decide which are the most important. Ad hoc requests can be a nuisance for customer satisfaction. But you need to learn how to handle these requests so your team doesn't get overwhelmed.
FAQ
What is a basic management tool used in decision-making?
A decision matrix, a simple yet powerful tool for managers to make decisions, is the best. It allows them to consider all possible solutions.
A decision matrix is a way of representing alternatives as rows and columns. This allows one to see how each alternative impacts other options.
This example shows four options, each represented by the boxes on either side of the matrix. Each box represents an option. The top row depicts the current status quo, while the bottom row represents what would happen if no action was taken.
The middle column displays the impact of selecting Option 1. It would increase sales by $2 million to 3 million in this instance.
These are the results of selecting Options 2 or 3. These are positive changes - they increase sales by $1 million and $500 thousand respectively. They also have negative consequences. Option 2 can increase costs by $100 million, while Option 3 can reduce profits by $200,000.
The last column shows you the results of Option 4. This will result in sales falling by $1,000,000
The best thing about using a decision matrix is that you don't need to remember which numbers go where. Simply look at the cells to instantly determine if one choice is better than the other.
The matrix already does all the work. It's simply a matter of comparing the numbers in the relevant cells.
Here is an example how you might use the decision matrix in your company.
You want to decide whether or not to invest more money into advertising. You'll be able increase your monthly revenue by $5000 if you do. You will still have to pay $10000 per month in additional expenses.
If you look at the cell that says "Advertising", you can see the number $15,000. Advertising is more valuable than its costs.
What does Six Sigma mean?
Six Sigma uses statistical analysis for problems to be found, measured, analyzed root causes, corrected, and learned from.
The first step to solving the problem is to identify it.
Next, data are collected and analyzed in order to identify patterns and trends.
The problem can then be fixed by taking corrective measures.
Finally, data will be reanalyzed to determine if there is an issue.
This continues until you solve the problem.
What are the four major functions of Management?
Management is responsible to plan, organize, direct, and control people and resources. It also includes developing policies and procedures and setting goals.
Management helps an organization achieve its objectives by providing direction, coordination, control, leadership, motivation, supervision, training, and evaluation.
The following are the four core functions of management
Planning – Planning involves deciding what needs to happen.
Organizing - Organization involves deciding what should be done.
Directing - Directing means getting people to follow instructions.
Controlling - Controlling means ensuring that people carry out tasks according to plan.
What are some common mistakes managers make?
Managers can make their jobs more difficult than necessary.
They may not assign enough responsibilities to staff members and provide them with inadequate support.
A majority of managers lack the communication skills needed to motivate their team and lead them.
Managers can set unrealistic expectations for their employees.
Managers might try to solve every problem by themselves rather than delegating the responsibility.
Statistics
- The profession is expected to grow 7% by 2028, a bit faster than the national average. (wgu.edu)
- Hire the top business lawyers and save up to 60% on legal fees (upcounsel.com)
- As of 2020, personal bankers or tellers make an average of $32,620 per year, according to the BLS. (wgu.edu)
- Your choice in Step 5 may very likely be the same or similar to the alternative you placed at the top of your list at the end of Step 4. (umassd.edu)
- 100% of the courses are offered online, and no campus visits are required — a big time-saver for you. (online.uc.edu)
External Links
How To
What is Lean Manufacturing?
Lean Manufacturing processes are used to reduce waste and improve efficiency through structured methods. These processes were created by Toyota Motor Corporation, Japan in the 1980s. It was designed to produce high-quality products at lower prices while maintaining their quality. Lean manufacturing seeks to eliminate unnecessary steps and activities in the production process. It is made up of five elements: continuous improvement, continuous improvement, just in-time, continuous change, and 5S. It is a system that produces only the product the customer requests without additional work. Continuous improvement is the continuous improvement of existing processes. Just-in time refers to components and materials being delivered right at the place they are needed. Kaizen means continuous improvement, which is achieved by implementing small changes continuously. Five-S stands for sort. It is also the acronym for shine, standardize (standardize), and sustain. These five elements can be combined to achieve the best possible results.
Lean Production System
Six key concepts make up the lean manufacturing system.
-
Flow - The focus is on moving information and material as close as possible to customers.
-
Value stream mapping - Break down each stage in a process into distinct tasks and create an overview of the whole process.
-
Five S's – Sort, Put In Order Shine, Standardize and Sustain
-
Kanban - visual cues such as stickers or colored tape can be used to track inventory.
-
Theory of constraints: Identify bottlenecks and use lean tools such as kanban boards to eliminate them.
-
Just-intime - Order components and materials at your location right on the spot.
-
Continuous improvement - incremental improvements are made to the process, not a complete overhaul.