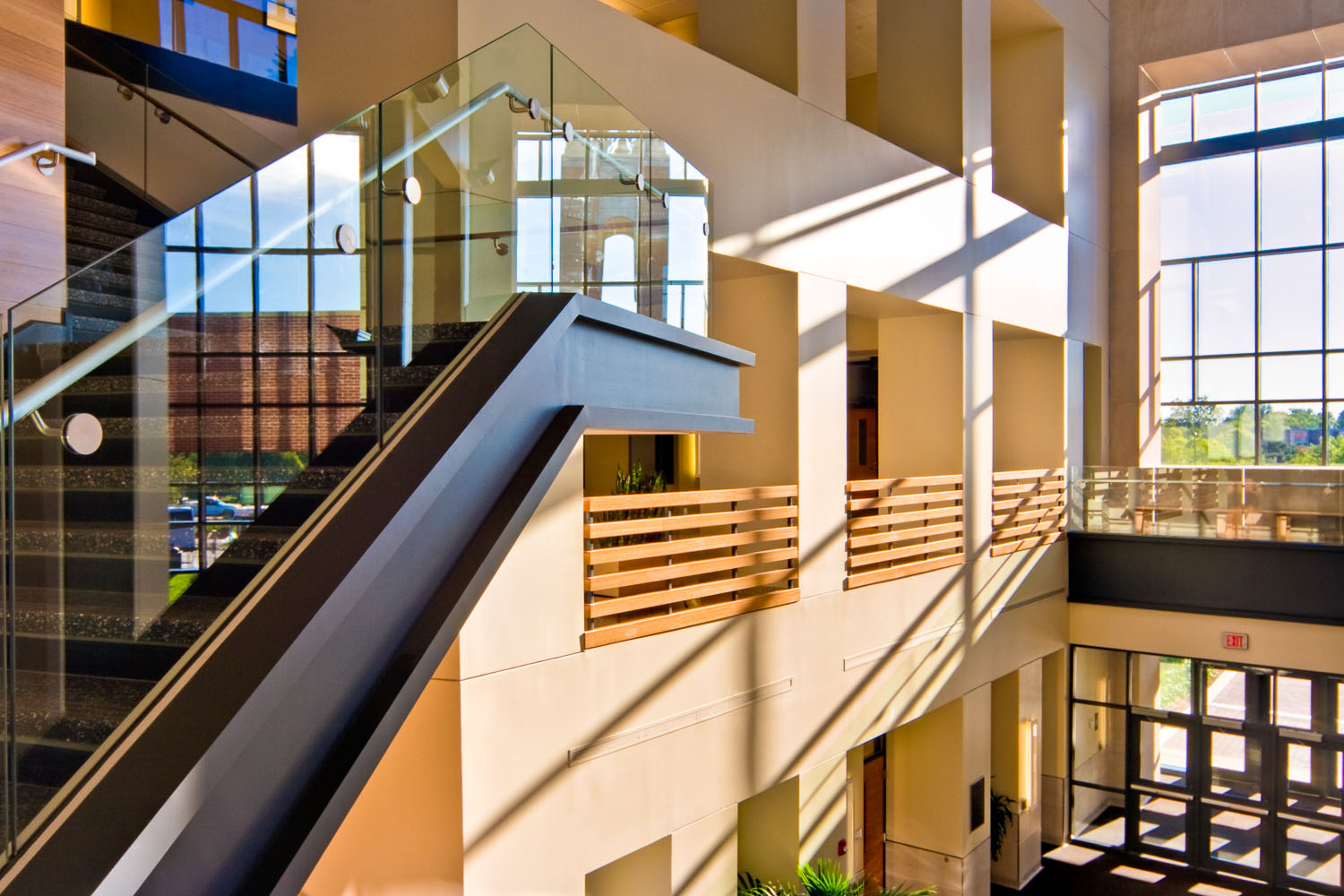
Supply Chain Management Review (SCMR), an American business management magazine, covers supply chain trends. It provides a broad overview of the supply chain and the role played by suppliers and manufacturers. The magazine provides a detailed look at current technology and trends. Visit SCMR's website for more information. You can now download the latest edition. Subscribe to the magazine for industry insight today.
Autonomous mobile robots
Autonomous Mobile Robots (AMRs) are a growing trend in warehouse automation, and their introduction is likely to make a big impact on many aspects of the supply chain. These robots have the ability to create their own routes and operate in dynamic environments. AMRs also make it easier to pick up objects manually, which leads to better productivity. AMRs are able to significantly lower labor costs and increase productivity by eliminating the need for manual moving.
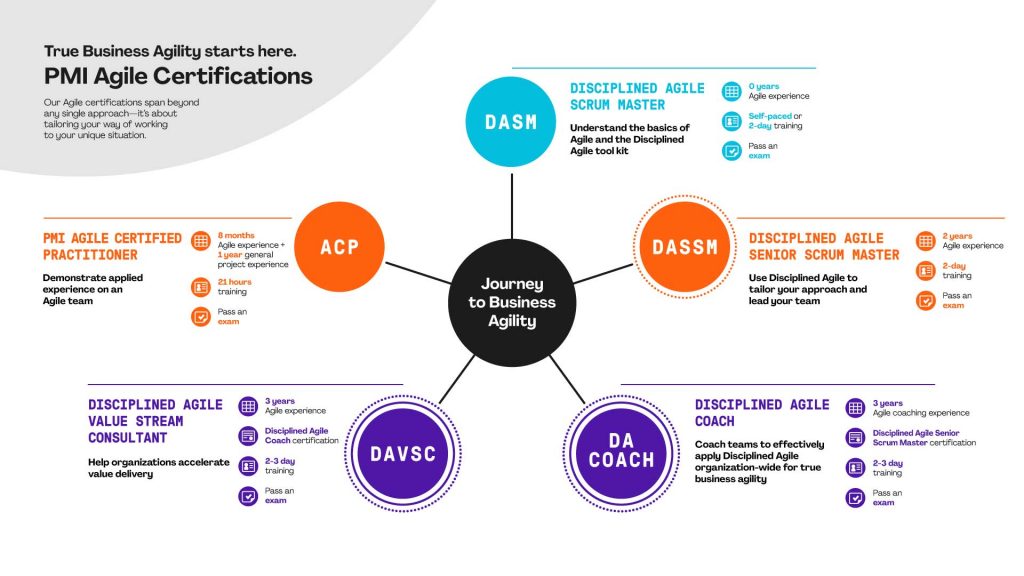
Blockchain
Supply chain management has become essential to a company’s success. Companies need to be responsive, flexible, and agile in order to stay competitive. They can differentiate themselves through continuous innovation. To realize these goals, it's important to improve the efficiency and effectiveness of the entire supply chain. One way to achieve this is with blockchain technology. Similar to a Google document, blockchain can be shared by many users, enabling them to make changes in real time.
Real-time data
The supply chain management landscape is rapidly changing. Real-time data can be used to help supply chain managers better manage their businesses. Companies can track and control inventory levels to prevent overages. Retailers can also use real-time reporting to anticipate and respond quickly to shipping delays. This will improve customer satisfaction. The best way to increase business productivity is to use real time data to manage inventory or make future decisions.
S&OP
Supply Chain Management Review has the latest news on supply chain management. This U.S.-based business magazine covers a variety topics, including global trends. The magazine also offers information about supply chain management tools and techniques. It is crucial to keep up with the latest trends in supply chain management for a company's success. In addition to reporting on the latest trends in supply chain management, the magazine offers advice on how to improve business operations.
Adapting to Change
Business owners must be able to adapt to changes in their supply chain management. The recent pandemic caused severe disruption to supply chains all over the world. There were long shut downs as a result of efforts to contain it. The sudden shocks that can affect supply chains, such as the 9/11 terrorist attack, strikes by dockworkers, and the SARS outbreak, have made them more vulnerable. Despite the complexity in supply chains most companies aren't equipped to deal with an emergency. Companies forget contingency plans and leave their supply chains vulnerable to disruption.
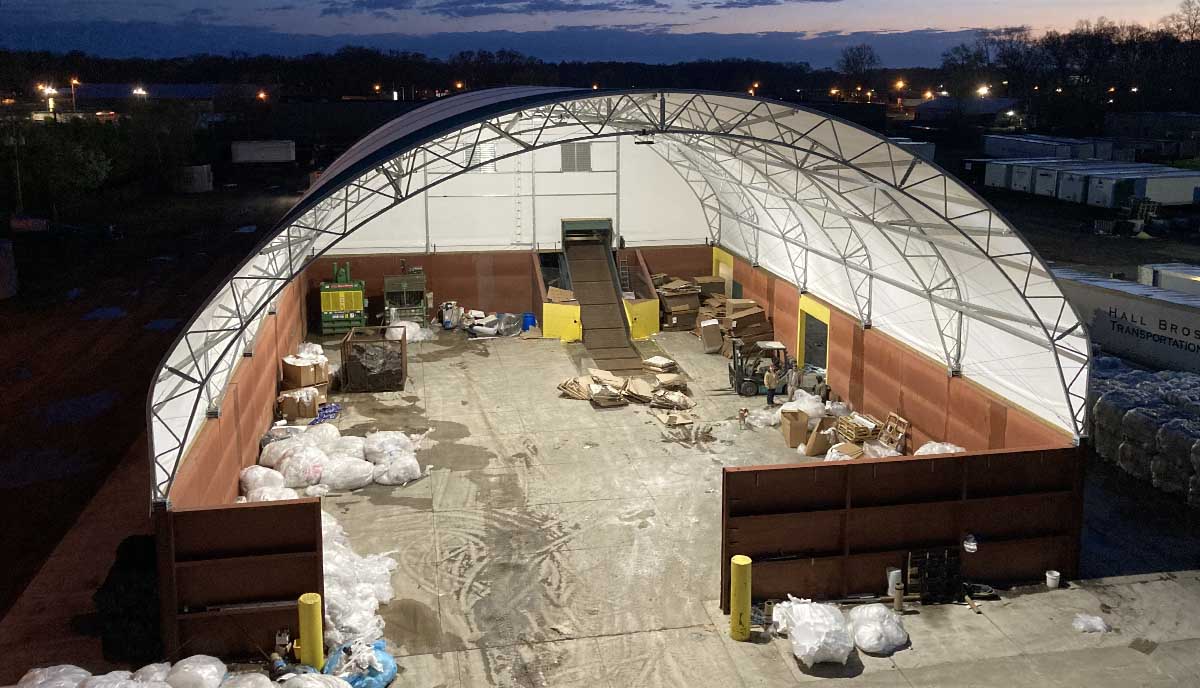
Supply Chain Management Goals
Organizations can improve their ability respond to changes by having their supply chain management reviewed. Supply chains are cross-functional processes that move raw materials into and out of a business. These processes include the management of inventory, transportation, and returns. The goal is to minimize disruptions and increase flexibility. Understanding the impact of these changes on profits is important. To learn how a supply chain management review can benefit your business, read on.
FAQ
What are the three basic management styles?
The three basic management styles are: authoritarian, laissez-faire, and participative. Each style has strengths and flaws. Which style do your prefer? Why?
Authoritarian - The leader sets the direction and expects everyone to comply with it. This style works best if the organization is large and stable.
Laissez faire - Each individual can decide for himself/herself. This approach works best in small, dynamic organizations.
Participative - Leaders listen to all ideas and suggestions. This style is most effective in smaller organizations, where everyone feels valued.
What are some common mistakes managers make when managing people?
Sometimes, managers make their job more difficult than it is.
They may not assign enough responsibilities to staff members and provide them with inadequate support.
In addition, many managers lack the communication skills required to motivate and lead their teams.
Managers can set unrealistic expectations for their employees.
Managers may prefer to solve every problem for themselves than to delegate responsibility.
How can we make our company culture successful?
A culture of respect and value within a company is key to a productive culture.
It's built on three fundamental principles:
-
Everyone has something to contribute
-
Fair treatment of people is the goal
-
It is possible to have mutual respect between groups and individuals
These values reflect in how people behave. They will treat others with consideration and courtesy.
They will be respectful of the opinions of other people.
These people will inspire others to share thoughts and feelings.
Company culture also encourages open communication, collaboration, and cooperation.
People can freely express their opinions without fear or reprisal.
They are aware that mistakes can be accepted if they are treated honestly.
Finally, the company culture promotes honesty and integrity.
Everyone understands that the truth is always best.
Everyone knows that there are rules and regulations that apply to them.
Everyone does not expect to receive special treatment.
What are the main four functions of management
Management is responsible for planning, organizing, directing, and controlling people and resources. Management also involves setting goals and developing policies.
Management aids an organization in reaching its goals by providing direction and coordination, control, leadership motivation, supervision, training, evaluation, and leadership.
The four main functions of management are:
Planning - Planning involves determining what needs to be done.
Organizing – Organizing means deciding how to organize things.
Directing - Directing is when you get people to do what you ask.
Controlling - Controlling means ensuring that people carry out tasks according to plan.
What is Six Sigma?
It's a method for quality improvement that focuses on customer service as well as continuous learning. This is an approach to quality improvement that uses statistical techniques to eliminate defects.
Motorola invented Six Sigma in 1986 as part its efforts to improve manufacturing.
The idea quickly spread in the industry. Many organizations today use six-sigma methods to improve product design and production, delivery and customer service.
Statistics
- The average salary for financial advisors in 2021 is around $60,000 per year, with the top 10% of the profession making more than $111,000 per year. (wgu.edu)
- This field is expected to grow about 7% by 2028, a bit faster than the national average for job growth. (wgu.edu)
- Our program is 100% engineered for your success. (online.uc.edu)
- As of 2020, personal bankers or tellers make an average of $32,620 per year, according to the BLS. (wgu.edu)
- UpCounsel accepts only the top 5 percent of lawyers on its site. (upcounsel.com)
External Links
How To
What is Lean Manufacturing?
Lean Manufacturing uses structured methods to reduce waste, increase efficiency and reduce waste. They were developed in Japan by Toyota Motor Corporation (in the 1980s). The aim was to produce better quality products at lower costs. Lean manufacturing seeks to eliminate unnecessary steps and activities in the production process. It has five components: continuous improvement and pull systems; just-in time; continuous change; and kaizen (continuous innovation). The production of only what the customer needs without extra work is called pull systems. Continuous improvement is constantly improving upon existing processes. Just-intime refers the time components and materials arrive at the exact place where they are needed. Kaizen means continuous improvement, which is achieved by implementing small changes continuously. Last but not least, 5S is for sort. These five elements are used together to ensure the best possible results.
Lean Production System
Six key concepts are the basis of lean production:
-
Flow: The goal is to move material and information as close as possible from customers.
-
Value stream mapping - break down each stage of a process into discrete tasks and create a flowchart of the entire process;
-
Five S’s - Sorted, In Order. Shine. Standardize. And Sustain.
-
Kanban - visual cues such as stickers or colored tape can be used to track inventory.
-
Theory of constraints: Identify bottlenecks and use lean tools such as kanban boards to eliminate them.
-
Just-in Time - Send components and material directly to the point-of-use;
-
Continuous improvement is making incremental improvements to your process, rather than trying to overhaul it all at once.